XuperCoat™ for Best-in-Class Mould Wear Resistance and Product Quality in Slab, Bloom and Billet Casting
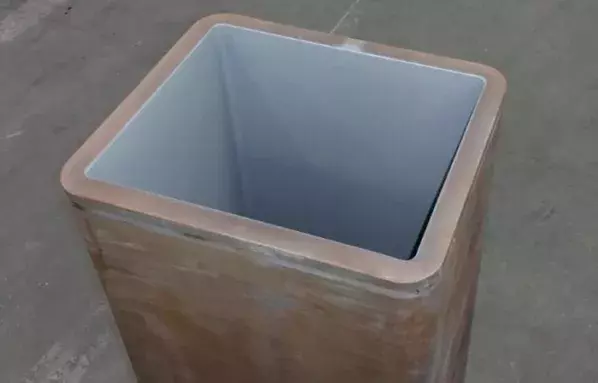
Mould coatings are a crucial part in continuously improving product quality and reducing operating cost in the continuous steel casting process. Monitor Coatings - a UK based Castolin Eutectic company first developed a unique, ceramic composite coating technology, XuperCoat™, which has produced best-in-class results in terms of mould life time, cast product quality and caster operating costs. 30 years of experience are a proven record for this coating type and continuous developments of the technology now allow to the application of such coatings on all types of moulds including bloom and billet tubes. Furthermore, with increasing environment restrictions on hexavalent chromium compounds XuperCoat™ is the most efficient reliable alternative for steel casters moving away from electroplating solutions.
In the late 1980’s Davy Distington, Workington (UK), commissioned the second slab caster for British Steel’s Port Talbot facility. The new caster featured a split mould enabling parallel casting of two strands using a central divider. However, due to the harsh environment the divider was worn far earlier than the rest of the mould even though it was being protected by an electroplating layer. It was then, that British Steel and Monitor Coatings came together to develop the very first, and until today, best wear protection coating for casting machine components such as mould plates, dividers and grid plates. Over those last 30 years Monitor Coatings and its customers in the steel industry have constantly worked together on enhancing this solution which is now available worldwide for all caster types and proving its superior performance day by day.
XuperCoat™ Technology – Cure to the Disease
XuperCoat™ is the next generation hard-metal composite coating using HVOF techniques capable of manipulating the coating composition to give an optimum microstructure design. This goes beyond the simple dual-phase alloys of tungsten carbide and cobalt to composite architectures. Significant performance improvements in coating properties have been achieved by changes in size, shape and distribution of the phases to produce ultra-fine-grained materials. Despite being very dense, coatings, even tungsten-based hard-metal coatings do not ultimately meet the corrosion- and abrasion-requirements of specific steel industry applications. Micro-porosity (pore size smaller than 5μm) in the coatings can lead to crack initiation. To combat this phenomenon, specialist coatings are also used to densify the underlying coating, forming a physical barrier between the component and the working environment. Unique, thermo-chemically formed ceramic coatings are subsequently formed, where a metal oxide bond is established not only between the particulate materials, grains or powders used to form the coating, but also between the coating and the substrate.
Monitor Coatings’ customers reported yield increases in cast steel on the same mould in the range of 2 to 8 fold compared to electroplating solutions. The actual mould’s life time increase varies dependent on the mode of operation and the nature of the product. Some plants operate thin slab casters or produce stainless steel, which tend to run on higher casting speeds and requires different coating setups compared to the low-speed traditional slab casters.
In addition to increased yield with no operation disturbances noted, even on high casting speed, customers identified additional benefits of the application of XuperCoat™ mould coatings, such as:
Improved product quality:
- Less star and corner crack defects
- Less strand shape issues
- Less stickers and sticker breakouts
Reduced operating cost:
- Lower consumption of copper moulds
- Lower consumption of mould flux powder
- Better economy of scale due to less wear-related enforced stoppages
Check out article in Steel Times International