4Rs of Recycling: Reduce, Reuse, Recycle and Repair
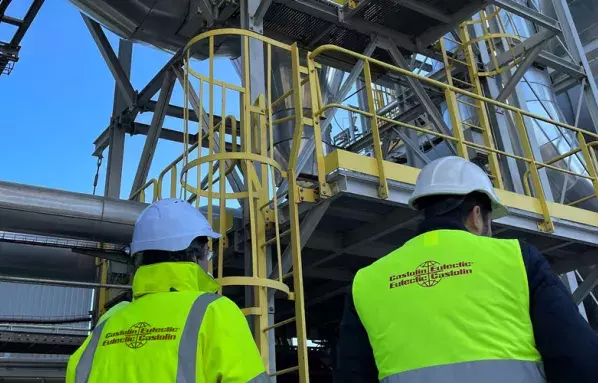
Businesses in the recycling industry can substantially reduce their costs – both financial and environmental – by wearfacing their equipment. Inaki Ezpeleta, Global Business Development Manager for Recycling at Castolin Eutectic, highlights the main wear-related challenges and advanced wear management solutions available.
Legislative and public demand for greater recycling effort is intensifying. Most people recognise that simply discarding used items is a waste of natural resources. They also appreciate that manufacture of replacements for discarded items means using extra energy and emitting more CO2. These costs are even greater when the manufacturing chain begins with new rather than recycled materials.
Difficult market conditions
Recycling is fundamental to sustainability, but to be viable as a business activity it needs to make a profit. That can be difficult for various reasons. One is the wildly fluctuating value of recycled materials. The price of copper or aluminium, for example, can drop suddenly, making its recycling less profitable or even non-viable.
Heavy duties and harsh forces
To understand how wearfacing addresses these problems, we must first look at the nature, function and operating conditions of machinery. Although recycling is a complex, multi-segmented industry, there are common processes which apply to each specialised area. These include:
-
Collection of materials and transport to the recycling site
-
Transport/movement of materials within the site
-
Crushing and/or shredding to the size required for the next process
-
Sorting into different material streams
-
Further processing – including refining
-
Supply of recycled raw material to manufacturers/users in the condition required.
The true cost of wear
Replacement of worn parts is costly. Managers must consider not only the price of the new part but the cost of labour to fit it and the loss of income while the machine is out of action. Lost output is even higher in the case of unplanned downtime due to failure of a worn component during operation. All these costs can be reduced by extending component life through wearfacing – or hardfacing as it is sometimes known.
Comprehensive wear management solutions
For many of the equipment surfaces described, a simple protective approach is to line them with steel CDP wear plates. These are hardened with alloys and can be applied, for instance, to line bulldozer and grab buckets, conveyor sides, chutes and any other containment or transport surface in the recycling plant.
Highly resistant to abrasion, impact and vibration, these types of wear plate typically last five times longer than OEM linings. They can be easily cut, shaped and fitted to protect any surface with screws, rivets or spot welding. Where required, plates can be supplied as standard plates or as pre-cut and formed sections matched to the equipment’s size and shape. This latter point is particularly important when lining the cylindrical or conical parts of a cyclone, or the inner surfaces of glass crushing, grinding and mixing machines.
Pipework requires another ready-made solution in the form of tube sections, elbows and Y-joints with alloy-reinforced lining. Known as CastoTubes, various diameters and section lengths are available, and assembly is simple.
When it comes to the crushing and cutting elements of crushers and shredders, a range of alloy and polymer wearfacing coatings (called MeCaTec at Castolin Eutectic) and welding wires can be applied to reinforce surfaces. Ideally, they should be applied from new, as a preventive measure, but in some cases they can be used in repair and restoration.
Technical Application Specialists ready to help
Specialist wearfacing products can be bought for use by a customer’s own engineers or applied by the company’s field engineers, who can also be called on for advice, assessment of wear problems, recommendation of solutions, and training around the world. It’s even possible to compare alternative solutions using Castolin Eutectic’s EcoTest calculator, which shows the savings in cost, and CO2 emissions for proposed wear protection solutions. This type of advice from suppliers often becomes more valuable over time as the external experts become familiar with the equipment and its health and maintenance history.