Nachhaltige Verschleißschutzlösungen verkürzen die Ausfallzeiten von Zellstoff- und Papierfabriken
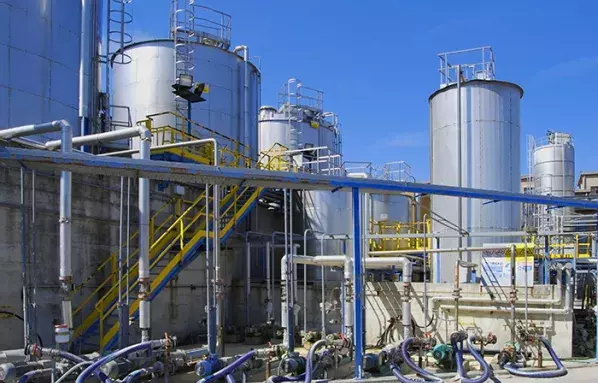
Der Verschleiß wichtiger Maschinenkomponenten ist ein wichtiges Thema für die Zellstoff- und Papierindustrie. Er führt zu zusätzlichen Kosten für Reparaturen, Ersatz und laufende Wartung sowie zu Produktionsausfällen.
Zellstoff- und Papiermaschinen sind verschiedenen Arten von Verschleiß ausgesetzt, wie Abrieb, Aufprall, Erosion, Ermüdung, Korrosion, Hitze und Kombinationen davon. Seit 1906 entwickelt und verwendet Castolin Eutectic innovative Verschleißlösungen für alle Aspekte des Prozesses, vom Holzplatz bis hin zum Service in der Fabrik. Dieser Ansatz ist integraler Bestandteil der Philosophie von Pioneering Industrial Sustainability, denn wenn kritische Anlagen optimal funktionieren, verbrauchen sie weniger Energie. Daher kann der Verschleißschutz den Betreibern von Zellstoff- und Papierfabriken nicht nur helfen, ihre Produktivität zu steigern, sondern auch die Energieeffizienz zu verbessern und ihren CO2-Fußabdruck zu verringern.
In diesem Artikel werden die praktischen Vorteile des Verschleißschutzes bei wichtigen Prozessen in der Zellstoff- und Papierproduktion erläutert.
Holzplatz-Fördersystem
Das Kettenrad der Förderkette ist ein Schlüsselelement des Holzplatz-Fördersystems. Die Zähne des Kettenrads sind einem hohen Verschleiß durch lose Rinde, Schmutz und Sand ausgesetzt. Ausfallzeiten des Förderers sind sehr kostspielig, da die Hackschnitzelproduktion gestoppt wird. Der Aufbau der Zähne mit zwei verschiedenen Lagen Schweißdraht, wobei die untere Lage für Schlagfestigkeit und die obere Lage für Abriebfestigkeit ausgelegt ist, verringert den Verschleiß erheblich. Es ist jedoch wichtig sicherzustellen, dass die Auflage weicher ist als die Kette, um Verschleiß an der Kette zu vermeiden. Diese Lösung kann die Lebensdauer des Kettenrads um 200% verlängern.
Die Glieder der Kette selbst verschleißen oben durch Abrieb, was zu einem Abrutschen der Stämme auf dem Förderband führt. Im Winter, wenn Frost und Eis auf den Stämmen liegen, ist dies noch viel schlimmer. Diesem Problem kann man begegnen, indem man jedes Glied mit einer Einschmelzlegierung beschichtet, die eine Mischung aus grobem Wolframkarbiden und Nickelbasislegierungspulver enthält. Das Ergebnis ist eine harte, verschleißfeste Beschichtung, die ideal ist, wenn eine griffige, rutschfeste Oberfläche erforderlich ist. Es ist bekannt, dass diese Lösung mehr als fünf Jahre hält, ohne Anzeichen von Verschleiß oder mangelnder Traktion.
Mulchen
Die Holz- und Papierindustrie verwendet die Rinde und die Holzabfälle aus der Entrindung auf verschiedene Weise. Für die Rindenaufbereitung werden Hammermühlen, Förderbänder, Förderschnecken und Ventilatoren eingesetzt. All diese Geräte werden durch die abrasive Wirkung der Rinde und der Holzabfälle abgenutzt.
An einigen Standorten werden Zerkleinerungsmaschinen eingesetzt, bei denen die Hammerspitzen durch das Zerkleinern von Rinde und Holz am stärksten beansprucht werden. Fremdmaterial wie Nägel, Draht usw. verursachen zusätzlichen Verschleiß. Die Wiederherstellung der Spitzen durch Schweißen und Beschichtung mit Pulver kann die Lebensdauer der Spitzen um über 100% erhöhen.
Bei anderen Anlagen mit Rindenzerkleinerungsmaschinen kommt es zu einer schnellen Abnutzung der Auswurfleiste am Ausgang. Sie nutzt sich aufgrund des hohen Abriebs und der Erosion schnell ab. In einem Fall wurde die ursprüngliche, aus verschleißfestem Stahl gefertigte Platte durch eine CDP® (CastoDur Diamond Plate)-Lösung auf der Basis von bi-metallischen Verbundwerkstoffen ersetzt, was die Lebensdauer um 200 % erhöhte.
Spänetransport und Zyklone
In den Mühlen werden die Späne in der Regel entweder pneumatisch in Rohren oder auf Förderbändern transportiert. Auch andere Systeme wie Ketten- und Schneckenförderer werden für den Transport von Spänen verwendet, allerdings in der Regel über relativ kurze Strecken.
In einem Fall wurde starke Erosion an einem Hubrohr festgestellt, das sich am Ausgang des Hackers zum Zyklon befindet. Obwohl verschleißfester Stahl verwendet worden war, stellte ein Kunde fest, dass die Einheit vorzeitig ausfiel. Ein Ersatz wurde unter Verwendung von CDP-Verschleißblech neu angefertigt. Die äußeren Seitenkanten wurden mit einem Eisenprofil verstärkt und mit einem speziell ausgewählten Draht verschweißt. Die inneren Schweißnähte wurden ebenfalls mit einem Schweißdraht hart geschweißt. Das Ergebnis war eine um 400% erhöhte Lebensdauer.
Auch die Laufräder der Ventilatoren leiden unter starkem erosiven Verschleiß durch die Mischung aus Holz, Sand und Staub im Luftstrom. Dies führt bei jeder Reparatur zu kostspieligen Ausfallzeiten, da sie mit einem Kran zerlegt werden müssen. Für eine Reparatur, bei der sich herausstellte, dass der Verschleiß sehr lokal begrenzt war, wurden maßgeschneiderte CDP-Verschleißplattenstreifen zugeschnitten und entsprechend geformt. Diese wurden dann schnell und einfach an die Ventilatorflügel geschweißt. Die Verbindungsstellen wurden mit einer Schutzschicht überzogen. Nach zwei Jahren waren keine Verschleißerscheinungen mehr festzustellen, was eine deutliche Verlängerung der Lebensdauer des Ventilators bestätigt.
Absiebung und Lagerung
Späne akzeptabler Größe müssen von unter- und übergroßen Teilen getrennt werden, indem die Späne über eine Reihe von Sieben geleitet werden. Die übergroßen Späne werden auf ein Förderband abgeworfen, das sie zu einer Art Zerkleinerungsmaschine transportiert, wo sie auf eine kleinere Größe reduziert werden. In den letzten Jahren wurde die Dicke der Hackschnitzel als wichtige Variable für die Auflösung erkannt und moderne Scheiben- oder Rollensiebe, die nach Dicke sortieren, sind heute weithin als Industriestandard akzeptiert. Das bedeutet, dass der Verschleiß minimiert werden muss, um die Genauigkeit des Siebvorgangs zu erhalten.
Ein Spänesieb hat Scheiben mit Spitzen, die sich durch den Abrieb der Späne abnutzen. Bei übermäßiger Abnutzung würden große Späne in den Fermenter gelangen. Um eine verschlissene Einheit zu reparieren, wurden die Oberflächen der Spitzen geschliffen und Pulver durch ein Sprühschmelzverfahren aufgetragen. Diese Lösung ermöglichte eine Reparatur an Ort und Stelle, ohne dass das Gerät zerlegt, die Siebscheibe ausgebaut und ersetzt werden musste. Dies führte zu erheblichen Kosteneinsparungen, da die Ausfallzeiten reduziert wurden und kein Ersatzteil gekauft werden musste.
Zellstoffherstellung
Der Begriff Auflösung bezieht sich auf jeden Prozess, bei dem Holz zu einer faserigen Masse reduziert wird. Dies kann mechanisch, thermisch, chemisch oder durch Kombinationen dieser Verfahren geschehen.
Der Auslasskrümmer von Batch-Fermentern ist starker Korrosion, Erosion, Abrieb und Temperaturschocks durch Kochlauge, Zellstoff und Dampf ausgesetzt. In einem Beispiel wurden verschlissene Stellen im Krümmer und in den Rohrleitungen mit Schweißelektroden aufgearbeitet, die für kritisch beanspruchte Bereiche entwickelt wurden. Auch die Stirnseiten der Flansche wurden auf ähnliche Weise überzogen und nachbearbeitet. Dadurch konnte die Lebensdauer gegenüber dem ursprünglichen Krümmer um das Dreifache verlängert werden.
Waschen
Der gekochte Zellstoff aus den Kochern muss gewaschen werden, um die Restflüssigkeit zu entfernen, die den Zellstoff in den nachfolgenden Verarbeitungsschritten verunreinigen würde, und um die maximale Menge an verbrauchten Chemikalien bei minimaler Verdünnung zurückzugewinnen.
Korrosion und Metallermüdung führen dazu, dass die Wäschersiebe brechen und Risse bekommen. Bisher musste diese Komponente mit den damit verbundenen Demontage- und Ersatzkosten verschrottet werden. Als Alternative bietet die Verwendung eines Hartlots mit hohem Silbergehalt eine schnelle und starke Reparatur mit hoher Zugfestigkeit und niedriger Bindungstemperatur.
Bleichen
Modernes Bleichen wird durch eine kontinuierliche Abfolge von Prozessschritten erreicht, wobei in jedem Schritt unterschiedliche Chemikalien und Bedingungen verwendet werden, in der Regel mit einer Wäsche zwischen den Schritten. Die Waschmaschinen und Pumpen im Bleichprozess müssen aus hochlegierten Edelstählen, Nickellegierungen und Titan hergestellt werden. Die Kontrolle der chemischen Korrosion in der Bleichausrüstung ist ein ständiges Problem.
Eine besondere Herausforderung ist die Refinerscheibe, die an Spannungsrisskorrosion und Verschleiß im Übergangsbereich zwischen Scheibe und Zylinder leidet. Dies kann durch Sandstrahlen und anschließendes Lichtbogenspritzen mit einer Beschichtung auf Basis der Nickel-Chrom-Legierung 625 behoben werden.
Verarbeitung
In den meisten Zellstoff- und Papierprozessen ist eine Art von Stoffsortierung erforderlich, um übergroße, störende und unerwünschte Partikel aus den Fasern für die Papierherstellung zu entfernen. Die wichtigsten Arten von Stoffsortierern sind Vibrations-, Zentrifugal- und Drucksortierer (zentrifugal oder zentripetal). Sie alle beruhen auf einer Art perforierter Barriere, die die akzeptablen Fasern durchlässt und das unerwünschte Material aussortiert.
Die weitere Aufbereitung des Zellstoffs ist die Mahlung der Fasern. Für die Stoffaufbereitung werden hauptsächlich zwei Arten von kontinuierlichen Refinern verwendet: Scheibenrefiner und konische Refiner.
Der effiziente Transport des Stoffes durch die verschiedenen Verarbeitungsschritte ist das Herzstück einer Zellstoff- und Papierfabrik. Keine Fabrik kann ohne zuverlässige Pumpenanlagen erfolgreich arbeiten.
Eine Herausforderung stellt die Refinerwelle dar, bei der die Edelstahlhülse durch Abrieb von der Bundbuchse, die sie in Position hält, verschlissen ist. Dieser Verschleiß wird durch Korrosion beschleunigt. Dieses Problem kann gelöst werden, indem die Welle mit einer Metallpulverlegierung beschichtet wird, die entwickelt wurde, um Korrosion zu verhindern und die Reibung zu verringern. Die Lebensdauer kann aufgrund der überlegenen Härte, Korrosionsbeständigkeit und Gleiteigenschaften der Beschichtung um 300% erhöht werden.
Altpapier und Karton
Viele Zellstoff- und Papierfabriken verwenden recyceltes Papier und Karton als weitere Quelle für Zellstoff zur Papierherstellung. Einige Fabriken arbeiten ausschließlich mit recycelten Materialien. Der Abfall wird in einen Hydrapulper gegeben, eine vertikale Wanne mit einem sich drehenden Rotor im Boden. Der Rotor zerkleinert Papier und Pappe mit Wasser zu Zellstoff und eine perforierte Extraktionsplatte unter dem Rotor zieht die Fasern aus dem Behälter. Durch weitere Reinigung und Entflockung des Zellstoffs wird er für die Papierherstellung vorbereitet. Der Rotor im Hydrapulper ist einem hohen Verschleiß durch das Altpapier sowie durch Fremdkörper wie Steine und Metallschrott ausgesetzt.
In einem Fall war eine Reparatur des Laufrads am Boden des Tanks erforderlich. Die Produktionskapazität nimmt drastisch ab, wenn das Laufrad verschlissen ist. Für die Reparatur wurden kritische Bereiche durch Schweißen mit Elektroden geschützt, die entwickelt wurden, um einen kombinierten Schutz gegen Abrieb, Druck und moderate Stöße zu bieten. Neben der Verlängerung der Lebensdauer von 2 Wochen auf 5 Monate kann das Schweißen dreimal durchgeführt werden, um die Kosten weiter zu senken.
Kalköfen
Eine der größten Herausforderungen bei der Herstellung von Zellstoff war schon immer die Wartung und Betriebseffizienz der Kalköfen in der Kaustifizierungsanlage. Dabei handelt es sich um große, Drehrohröfen, mit einem Durchmesser von 4-6 Metern und einer Länge von 45-150 Metern. Da sie mit feuerfesten Schamottesteinen ausgekleidet sind, sich ständig auf Rollen drehen (in Abständen von etwa 5 Metern) und im Inneren auf 1450°C erhitzt werden, sind sie anfällig für ernsthafte Betriebs- und Wartungsprobleme. Je länger der Ofen ist, desto größer können diese Probleme sein, insbesondere im Hinblick auf Risse und eine falsche Ausrichtung der Rollen.
Eine erfolgreiche Reparatur wurde durch den Einsatz von Schweißelektroden mit geringer Wärmeentwicklung und einem streng kontrollierten Verfahren ermöglicht. Es wurden erhebliche Kosteneinsparungen erzielt, da kein neues Teil erforderlich war und die Ausfallzeit von 10 Wochen auf 2 Wochen reduziert werden konnte.
Reparatur und Überholung erzielen oft bessere Ergebnisse als Ersatz
Der erste Instinkt von Wartungsteams in der Zellstoff- und Papierindustrie besteht oft darin, verschlissene Teile durch brandneue Teile zu ersetzen. In dieser Branche ist jedoch die Kontinuität des Betriebs in der Regel das wichtigste Anliegen. Daher können sich Reparatur und Überholung in vielen Fällen als überlegen erweisen. Der Einsatz modernster Verschleißteile kann nicht nur eine schnellere Wiederherstellung der Betriebsbereitschaft gewährleisten, sondern auch die Lebensdauer erheblich verlängern, oft um ein Vielfaches. Das Ergebnis ist eine höhere Zuverlässigkeit, verbesserte Nachhaltigkeit und die bestmöglichen Gesamtbetriebskosten.