Industries
Sugar
Extend service life, maintain part profile, improve extraction, reduce downtime.
Choose a category
Discover other industries
Sharing our welding, brazing and coating know-how
Brochures
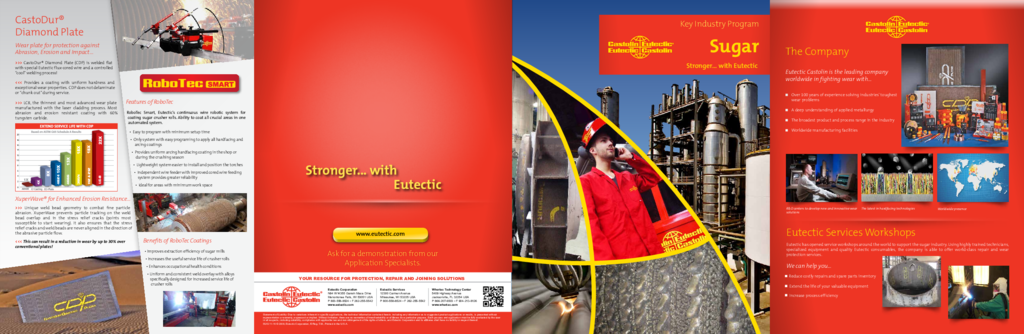
Sugar Industry applications
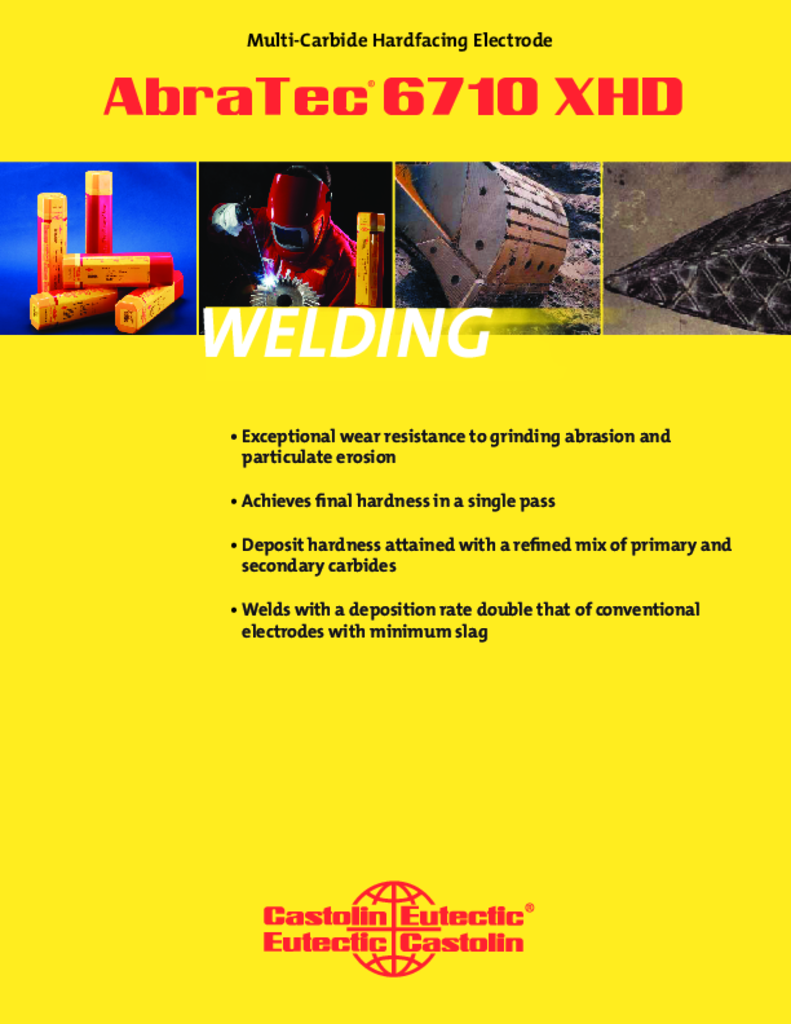
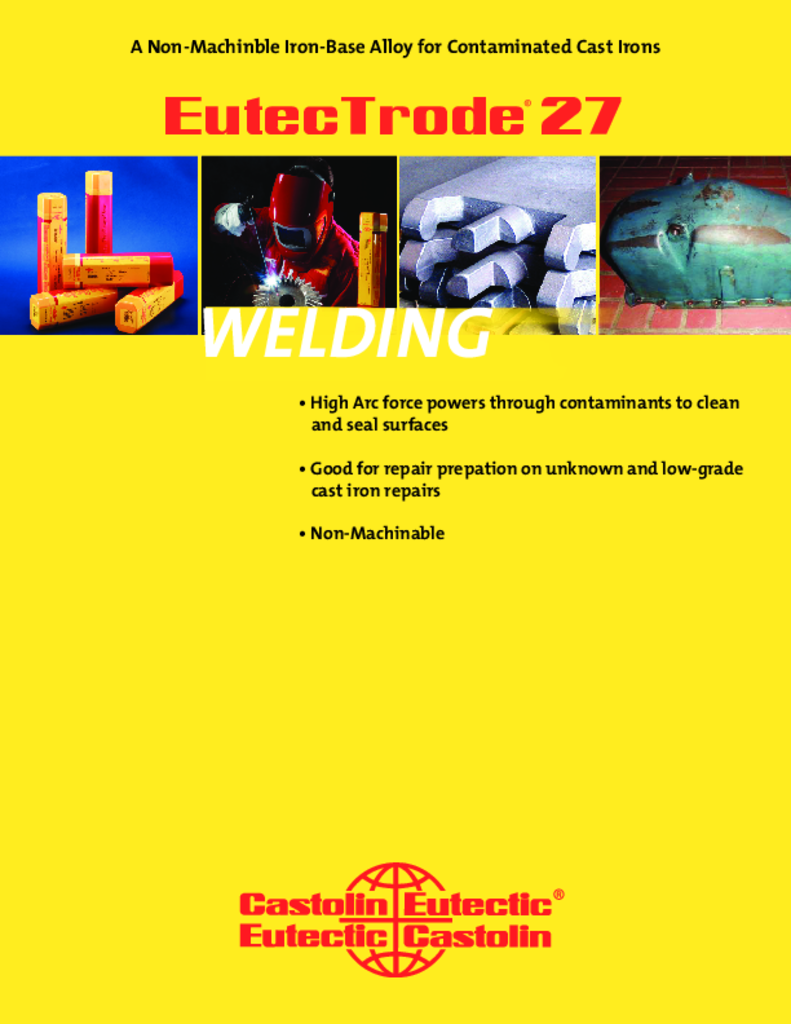
EutecTrode 27
Non-machinable electrode for contaminated and porous cast iron. Use as a buffering layer before using other electrodes.