Whertec: Challenging automated boiler panels project
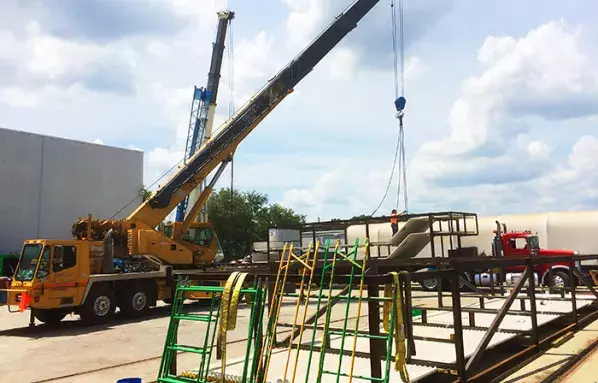
After several months of pursuit and great teamwork, Whertec was awarded one of their most challenging automated panel projects to date in August 2016. This job pushed their team’s capabilities and reinforced their reputation of being “The Reliability Experts”. Whertec received 567 m2 of boiler tube panels for sand blasting and ChromeClad™ coating at their Florida Technical Center.
The panels were fabricated in Finland and shipped to Whertec’s facility for a high pressurised recovery boiler. Each panel was 139.7 cm long and 26.67 cm wide. An average project for comparison is 101.6 cm long and 20.32 cm wide. The process began with sand-blasting each panel to SSPC-SP5/MACE#1 clean white metal before ChromeClad™ coating. While panel fabrication was in process, Whertec engineers designed their state-of-the-art automation system in order to accommodate the size and unique geometry of each panel. Each panel was configured with headers, bends, and various openings which required complicated and precise programming for the automation processes. The final phase took place onsite, with 58 m2 of field tie-ins and densification of all coated areas of installed panels with TubeArmor™.
This project was allotted 3 weeks for completion at the Florida Technical Center and 48 hours for the onsite tie-ins and densification. Both phases were accomplished safely, on time, within budget, and exceeded quality expectations. Whertec’s customer was extremely impressed with the professionalism, quality control, and execution. The project has led to discussions on two additional boiler overhauls starting as early as 2017.