Hardfacings extend life of sinter crusher components while saving energy & CO2
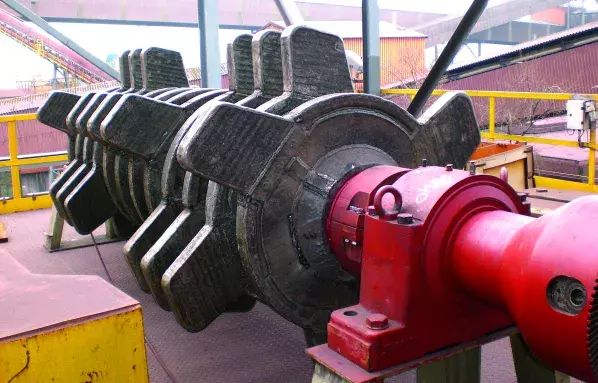
With a critical role at the heart of a mill’s operation, the sinter crusher is often key to profitability, therefore it is essential to take a proactive approach to maintenance. Martin Kirchgassner, Chief Technology Officer (CTO) of Castolin Eutectic, explains how hardfacing technology provides resilience for crusher components that experience heavy wear.
As the machines that break heavily abrasive sinter into suitably-sized pieces to feed the blast furnace, sinter crushers are exposed to extreme wear. Being hot, hard and abrasive, sinter is a challenging material to handle.
Wear is most strongly experienced in two main areas: the crusher bars and the teeth on the rotor. However, the chute that feeds material into the machine can also be affected as sinter falls through it, as can the sieves that grade material to extract the fines so that they can be used as feedstock to make more sinter.
The bars experience the most wear of all. They take the form of large rectangular steel bars in parallel like a comb, with each bar being 100 mm wide and up to 3 meters long. When sinter is fed into the crusher, it is picked up by the teeth on the spinning rotor. These feed and smash sinter into the bars, putting them under an intensive mechanical impact loading that may require maintenance as often as every six weeks.
The action also creates heavy wear on the rotor components. These typically include two to four teeth that pick up and handle the sinter, as well as discs that the teeth are mounted on. Typically, teeth may last under a year.
Traditional choices to combat wear
Various options are available for operators to consider reducing wear and therefore extending the life of a crusher. This maintains the mill’s output, leading to more efficient production. Traditionally, operators have several options to achieve this.
The first of these is to simply accept heavy wear rates and the regular outages required to overhaul components and rectify the wear. This makes use of breaker bars made from materials such as structural steel with high hardness to resist wear, such as alloy S275 or S355. Alternatively, manganese steel is often used for rotor teeth. This may be suitable for a crusher with relatively low wear rates.
However, for sites with more intensive wear due to higher temperatures, loading and the mechanical design, operators need to take actions to deploy increasing levels of wear resistance. As requirements increase, operators can consider fitting wear-resistant liners or inserts, applying wear-resistant hardfacing coatings, using wearplates and integrating water cooling into breaker bars.
When it comes to liners or inserts, these are typically made from matrix materials that contain cemented carbides. However, as wear levels increase, these may still experience rapid wear.
Therefore, the next tactic available is to apply a hardfacing coating to high-wear areas. On the rotor, these are typically the outer edges of the teeth and the disc body of the rotor, whereas the breaker bars require a significant 10-15 mm wear-resistant layer welded onto the top of the bars, as well as 5-8 mm on the edges.
This still may not achieve the intended benefits. For example, the coating on rotors might not provide adequate protection over base material, which can sometimes wear away first. Meanwhile, hardfacing coatings typically have a lower heat transfer coefficient than structural steel.
Therefore, applying a thick coating to breaker bars may have the unintended consequence of creating a build-up of heat. In turn, this may effectively decrease the wear resistance, enabling cracks to develop and propagate through the thick layer and causing spalling, where fragments of the outer layer of hardfacing are lost prematurely.
High-performance Castolin Eutectic solution
The challenge is that there is a limit to all of these solutions. Therefore, to protect availability of their sinter crushers, many mills opt for a high-performance hardfacing that is custom-designed for the precise wear rates experienced.
Using this type of solution can extend the service life of a crusher’s key components by a factor of three. This significantly extends the maintenance interval to reduce the frequency of maintenance outages while preserving the productivity of the mill as a whole.
The Castolin Eutectic approach uses alloys with extremely high wear resistance that can withstand temperatures of 400 °C and above. The key to success is the expertise in selecting the material and the use of an application technique that uses anchor points in the structural steel component, as well as a specific welding pattern that maximizes durability from a relatively thin coating.
Saving energy and emissions
While the main goal of a hardfacing coating is to extend the service life of crusher components, the components will retain their original geometry for longer. This leads to the secondary benefit that the machine will crush sinter for longer at the specified level of energy efficiency. In comparison, when components become worn and rounded, it takes extra energy to achieve the same crushing results.
In addition, extending the life of steel components saves the energy that would otherwise be required to make new crusher teeth or bars to replace worn parts.
Therefore, a hardfacing coating can be a tactic to reduce energy consumption and CO2 emissions, as well as protecting valuable uptime and mill efficiency.
Having developed this type of advanced coating system in 2013, it’s now been deployed at nine steel plants across Europe, either as a complete solution or as test components. One of these sites has tested the approach against a liner solution on different teeth on the same rotor disc.
As the solution traditionally used at the site, the customer’s normal experience was for the liner to have completely worn out and require replacement after 10 months in operation and production of 2.4 million tons of sinter.
Calculating the business case
The cost of a high-performance solution must be higher as it requires high quality raw materials, as well as expert engineering technicians to specify and apply them. However, it’s clear that they enable higher availability and lower downtime that provide financial savings. These can be significant for mills where the sinter plant is a mission-critical process step that influences overall output.
Calculating the investment case of a high-performance hardfacing is a complex calculation. It varies for each site, depending on loading of the system, whether enough sinter is kept in stock to ride through outages, and the cost and availability of alternative feedstock for the furnace.
It is important to secure a test sample that has been treated with the high-performance hardfacing and test it against the existing solution to fully understand and evaluate the comparative performance. This is factored into the business case through the required frequency of maintenance, as well as the cost of labour and parts, which depend on the extent of wear experienced, the size of the machine and the type of maintenance needed.
Boosting production efficiency
The sinter crusher is an important piece of equipment that experiences extensive wear and can influence a mill’s entire production output. Therefore, it may be worth investing in high-performance hardfacing coatings on key components such as crusher bars and teeth that withstand wear and maintain their shape for longer.
Even a modest improvement in service life has potential to reduce energy consumption and CO2 emissions thanks to components that keep their original shape. In addition, it can offer potential for significant cost savings with fewer stoppages for maintenance and more time in service.