Mining
Choose a category
-
ImageShearers and Augers
-
ImageCrushers
-
ImageDrag chain conveyor
-
ImageWear Polymers - MeCaTeC®
-
ImageLaserClad® Services
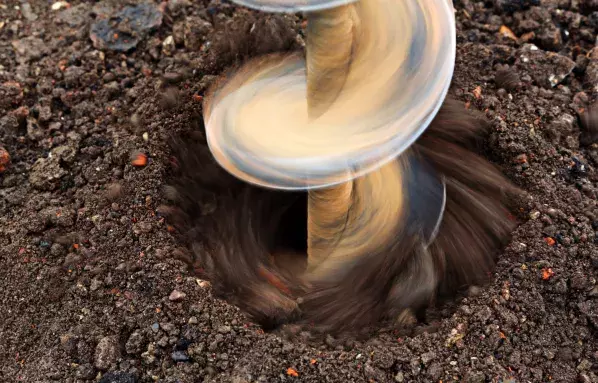
A cutting process using powerful rotating tools
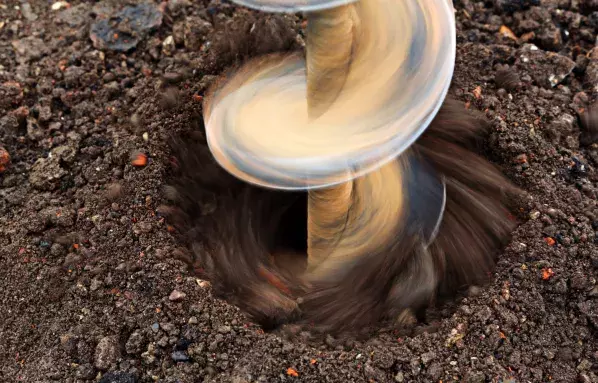
Drilling tools work with abrasive materials of different hardness, texture and dimension, like granite, quartz, basalt, gravel, etc. The main functioning of these engines vary depending if the work is done by percussion fragmentation of the compact ground layers that are less cleavable or by drilling and transporting through rotation of the material that is less compact and relatively cleavable.
These percussion tools (rods) generally sustain significant impact and abrasion. The choice of the alloys is therefore oriented to cold working deposits which are strain resistant.
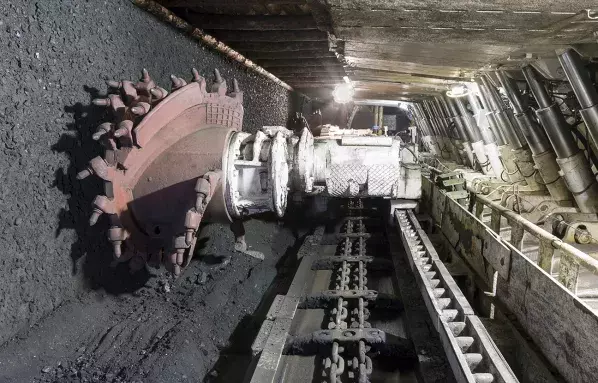
Give tools a second life
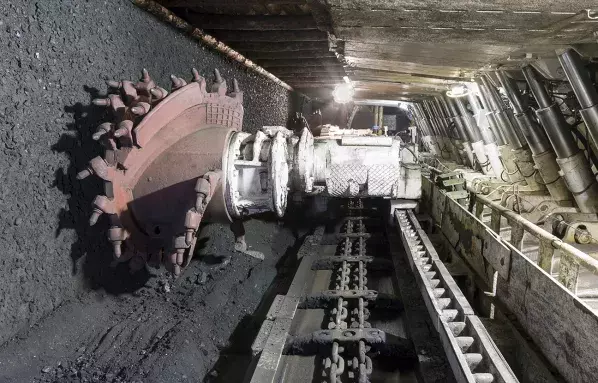
For tools cutting through rotation (auger, drill rod) the type of wear is mainly abrasion combined with weak pressure on the surface. The preferable choice is alloys having good wear resistance against medium impact and abrasion under weak pressure.
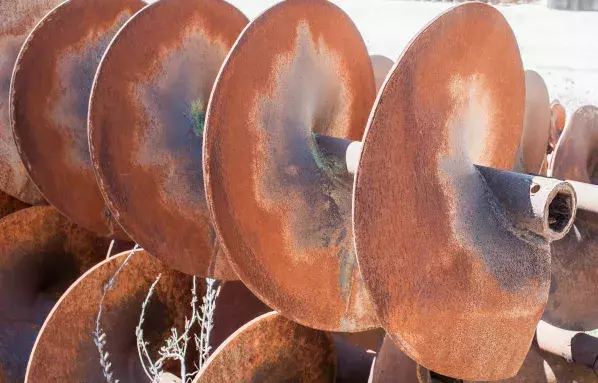
Alloy protection against chocks and abrasion
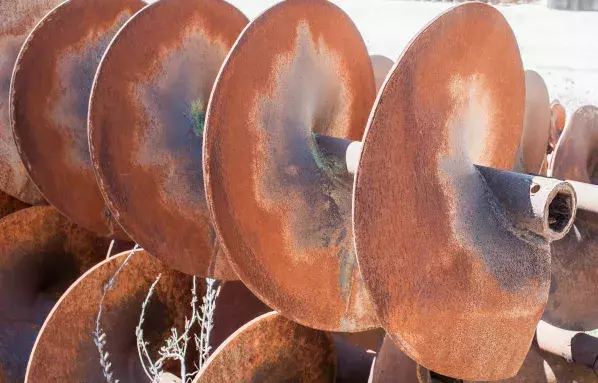
Each tool is specific and the operating conditions depend on the nature of the ground. Nevertheless, two application possibilities are generally observed:
The wear protection against abrasion with chrome cast iron type deposit alloy in cases where tools are not exposed to high impact.
Often, these tools are subject to impact that damage the protection beads. In this case a low alloy deposit is chosen containing tungsten carbide in a matrix which is less sensitive to impact.

CUTTING-EDGE LASER CLAD WEAR LINERS

Avoid equipment failures and drastically reduce downtime with the most lightweight wear protection available with superior surface hardness. CDP LaserClad® LC8 is the optimal choice for protecting mining parts exposed to high wear with minimum component stress, including mine ventilation fans, mine skips, conveying systems, and certain material handling systems.
Our laser clad wear plate is metallurgically bonded with wear-resistant proprietary alloys in an ultra-thin design. The powder becomes the sacrificial layer on the base plate, offering maximum protection at minimum weight.
- Superior surface hardness
Ease of handling and installation
Improved mine safety and work environment
Light-weight alternative with reduced energy consumption
Increased sustainability
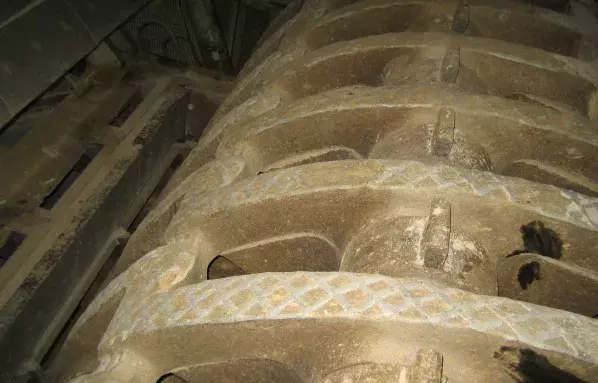
Subject to abrasion
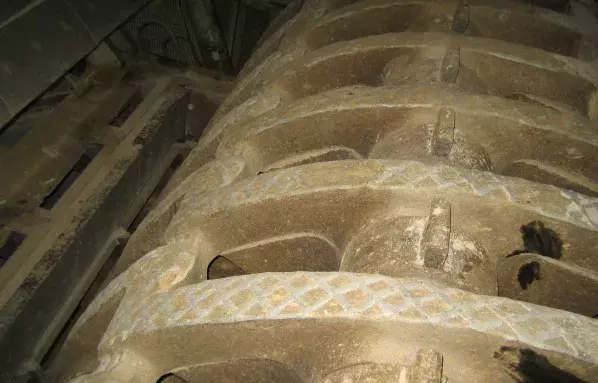
The rotor is the main part of the crusher, it provides the tightening of the beaters with help of the fixing elements. The mechanical welded disks are subject to abrasion due to the action of particles on the outer parts of the disk. A preventive coating is recommended on these parts as well as on the flanks.
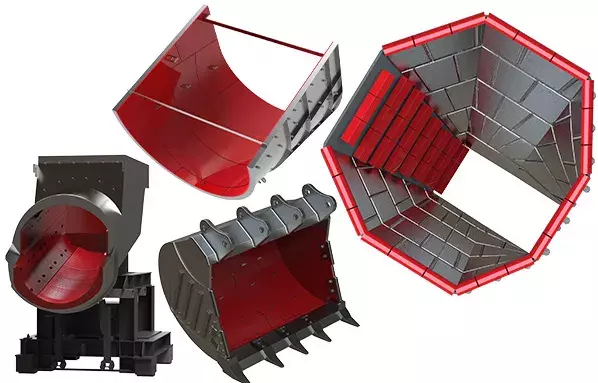
ENHANCE OVERALL WEAR LIFE WITH CASTOCHROME CASTINGS
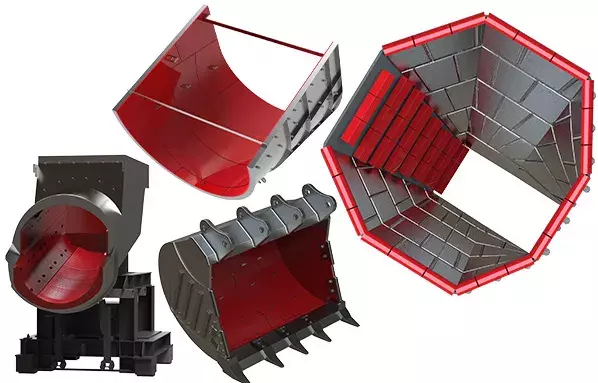
Fixed Plant
-
Mill feed & discharge chutes
-
Transfer & load-out chutes
-
Skip discharge chutes
-
Surge bins and receiving hoppers
-
Conveyor skirt liners
-
Vibratory and grizzly feeders
-
Apron & pan feeders
Mobile Plant:
-
Dragline buckets
-
Electric rope shovels
-
Wheel loader buckets
-
Dozer blades
-
Truck boxes
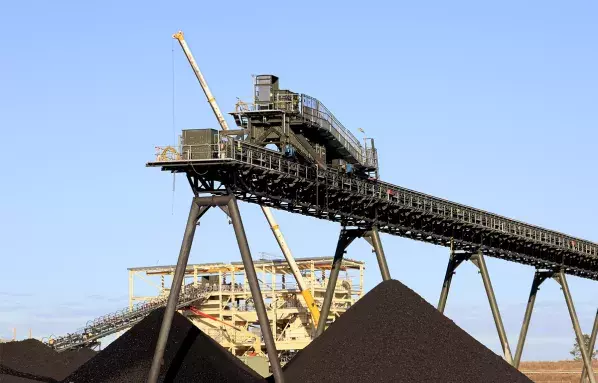
Avoid equipment failure
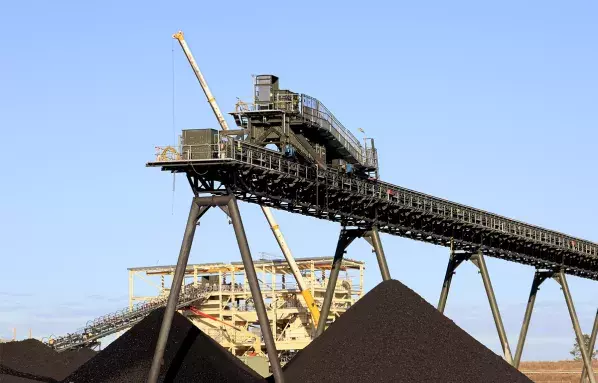
Drag chain conveyors are ideal to carry material such as wood, coal, lime or waste when a change in elevation is required and throughout very long distances. Unfortunately, the abrasive nature of transported materials negatively affects the equipment service life by
- wearing-out the conveyor surface,
- which increases the forces required to pull the chain.
Very frequently, high wear appears on the chain path. As a result, the surface is not smooth anymore, forces increase, the chain is damaged and parts must regularly be replaced to avoid equipment failure.
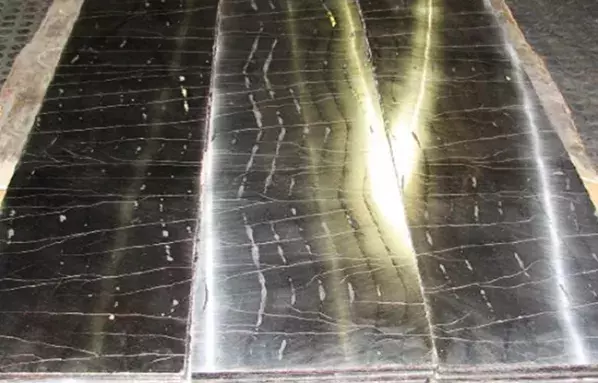
4 times more resistant than traditional hardened steel
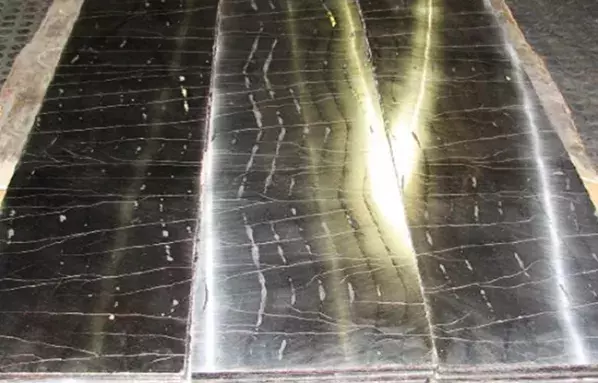
Dating many years back, at Castolin Eutectic we protect our customers’ conveyor surfaces with our well-known CDP® wearplates. Premium polished CDP® were also installed in cases where a low friction surface was required. Today, based on a similar concept, we offer the easy-to-install WSS that protect the chain path against severe abrasion and friction. WSS are a composite material made out of mild steel and a specific high wear resistant alloy with low friction coefficient. To ensure good sliding properties and reduce the chain conveyor energy consumption, the strip surface is polished. As a result, our strips are at least least 4 times more resistant than traditional hardened steel. Surfaces remain smoother for a longer period of time which eventually also reduces chain damage. WSS are also suitable for machines that need to sustain high forces and vibrations while working in abrasive environments.
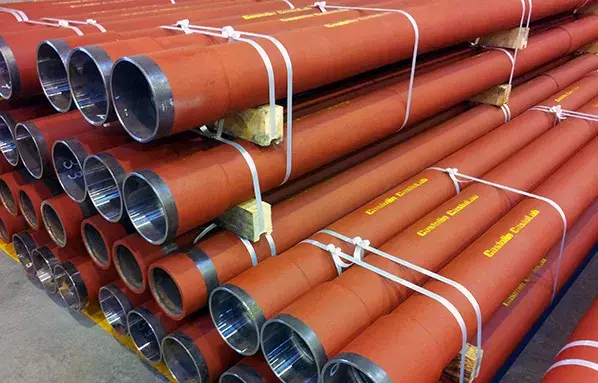
BENCHMARK BACKFILL SLURRY WEAR PERFORMANCE
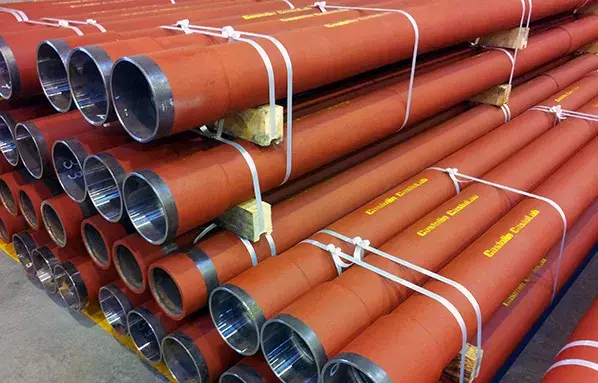
Where safety meets efficiency and productivity
-
Benchmark performance | Reduced cost per tonne ownership
-
Engineered pipe connections | Efficient retrofit and new installations
-
Process controlled cladding ensures superior performance
-
Technical support | Site-specific wear surveys and performance monitoring
-
Mine contractor grade offerings | Ease of installation & impact resistant formula
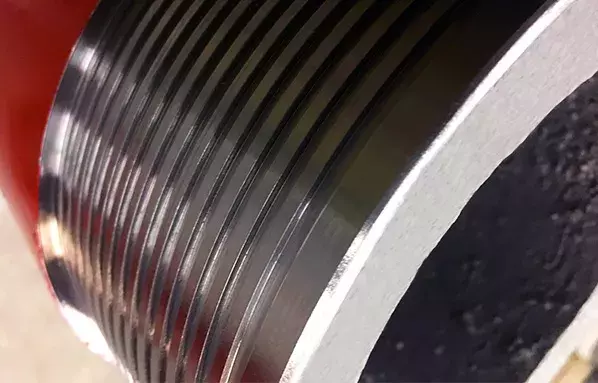
ECONOMICAL WEAR RESISTANT PIPES FOR SLURRY BACKFILL TRANSPORTATION
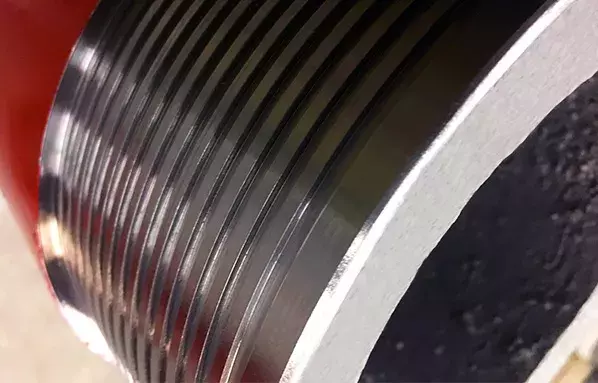
MeCaPipe is our economical alternative to CastoTube wear pipes. MeCaPipe incorporates the high-performing MeCaTeC lining technology to offer an alternative solution for general slurry applications. Combined with CastoTube, MeCaPipe can meet specific client requirements to provide the adequate level of protection against abrasion, erosion and corrosion. For a seamless wear performance, the lining thickness is typically selected based on the finished ID to match the existing piping system.
MeCaPipe is engineered to withstand slurry wear and erosion. It outlasts traditional piping materials, minimizing costly changeouts and providing enhanced performance and operational efficiency. MeCaPipe can be easily repaired or relined to prolong life.
Our team will work closely with your mine to deliver the right pipe lining solution to optimize your slurry backfill transportation systems.
Contact us for an expert wear pipe analysis.
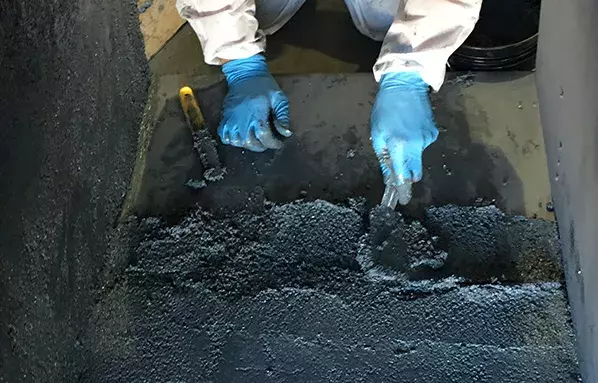
MINE-GRADE WEAR COMPOUNDS FOR ABRASION, EROSION AND CORROSION PROTECTION
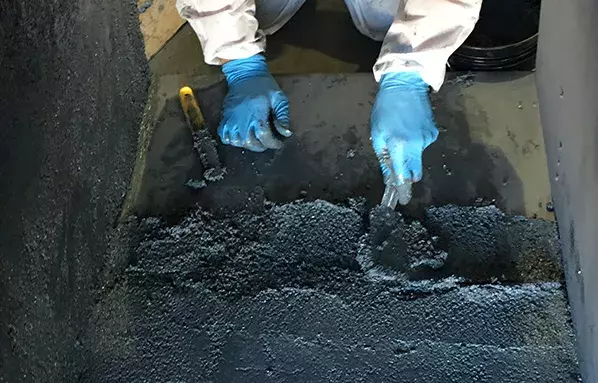
From repair and rebuild to corrosion resistant barrier coatings, MeCaTeC offers an industry-leading range of engineered polymers that will perform in the most demanding mining applications. MeCaTeC is the ideal solution for quick surface and part repair. It instantly bonds to the surface with no welding, becoming a sacrificial layer that provides abrasion and erosion protection. Its cold bonding feature eliminates the need for a Hot Work Permit.
MeCaTeC is the ultimate protection layer for the demanding resurfacing requirements. Protect your assets with MeCaTeC!
Typical Applications include:
-
Ceramic tile and rubber lining replacement
-
Cyclones, chutes, bins and transfer points
-
Pipe elbows and slurry pipes
-
Slurry pumps
-
Screw conveyors
-
Bag house
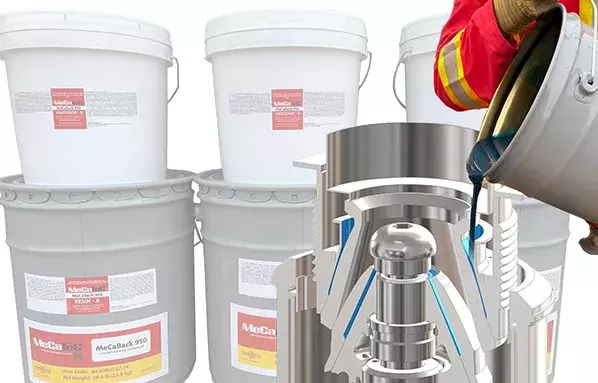
HIGH PERFORMANCE CRUSHER BACKING COMPOUNDS
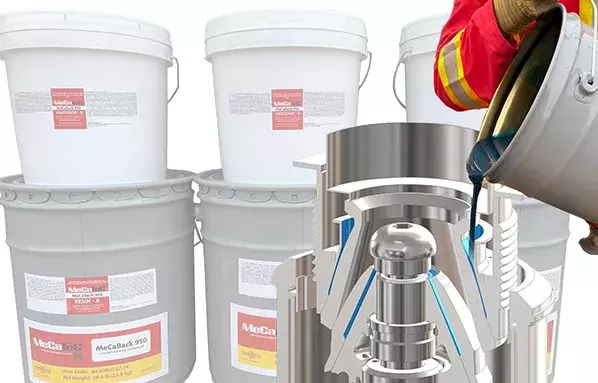
Crusher backing compounds are a cost-effective way to protect crushing machines from friction, vibration and wear.
Our innovative line of crusher backing compounds is specifically designed to reinforce the liner, fill voids, reduce vibration and eliminate friction in rock crushing heavy machinery. It is easily applied between both gyratory and cone crusher liners and the crusher body part.
MeCaBack is an excellent choice of a crusher compound for mining, mineral processing and aggregate equipment including:
-
Crushing machines
-
Cone & stone crushers
-
Grinding mill liners
-
Backing plates
-
Lock bushings
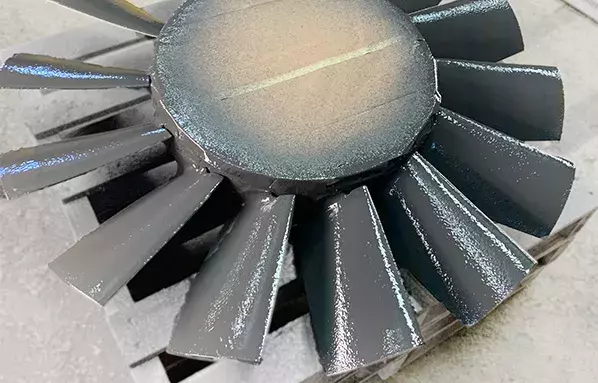
PERFECT COMBINATION OF SAFETY, PERFORMANCE AND COST SAVINGS
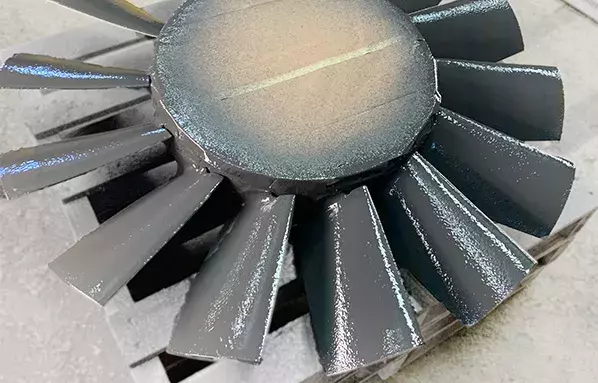
-
Proprietary formula with Kevlar fiber interlocking technology
-
Engineered ceramic fillers to maximize wear performance
-
Optimized packaging for faster mixing during shutdown repairs
-
Excellent alternative to replace ceramic tiles and rubber linings
-
Rapid-cure formula ensures a quick return to service
-
Easy to apply with trowel, brush, MeCaSpray gun, or airless spray
-
On-site Technical Support with industry-leading expertise and application know-how
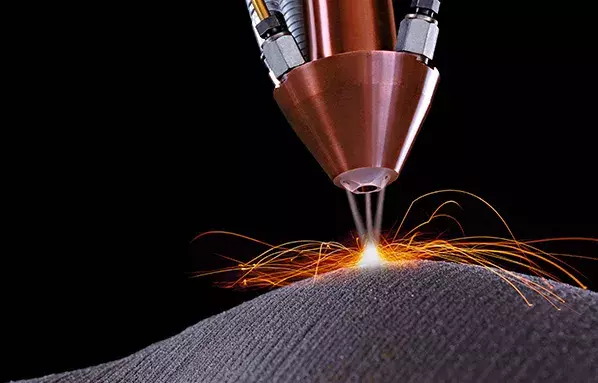
LASER CLAD OFFERS PRECISE, RELIABLE AND CONSISTENT PART PERFORMANCE
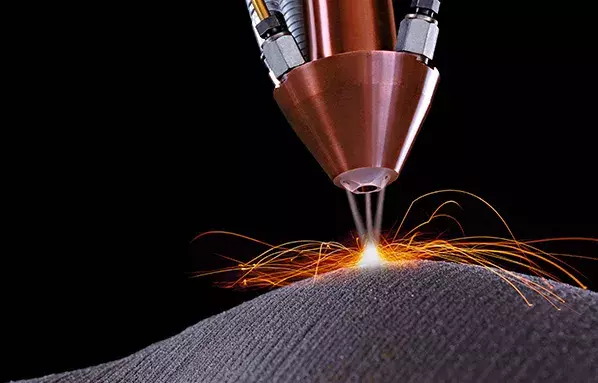
Mining equipment and components are exposed to the harshest wear conditions, compromising the overall performance of a mine site. Castolin Eutectic’s laser clad surface engineered solutions protect your valuable assets, maximizing operational service life, reducing changeouts and increasing site safety.
Our laser cladding process uses precision lasers to metallurgically bond high-performance material coatings to base materials. This modern engineered process is incredibly consistent, uniform, and reliable.
With an increased demand to incorporate smart mining practices and decrease the negative impact on the environment, laser clad is becoming an excellent alternative to hard chrome plating, thermal spray and PTAW.
Contact us to find out how you can leverage laser clad technology to protect your mine assets.

ADVANTAGES OF LASER CLADDING AT A GLANCE

Laser cladding is a cost-competitive alternative when compared to weld overlay, thermal spray and chrome plating.
- High surface quality with no or minimal post-machining
-
Exceptional durability, increased part repeatability and performance
-
Very low heat input and minimal part distortion
-
Metallurgical bond allows shock absorption
-
Unlimited overlay and substrate combinations
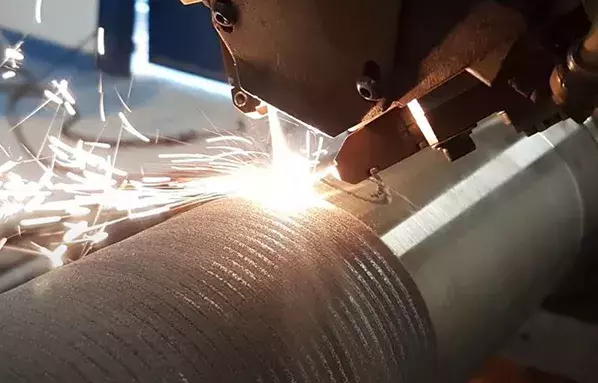
ENHANCE THE OPERATIONAL LIFE OF MINING EQUIPMENT AND COMPONENTS
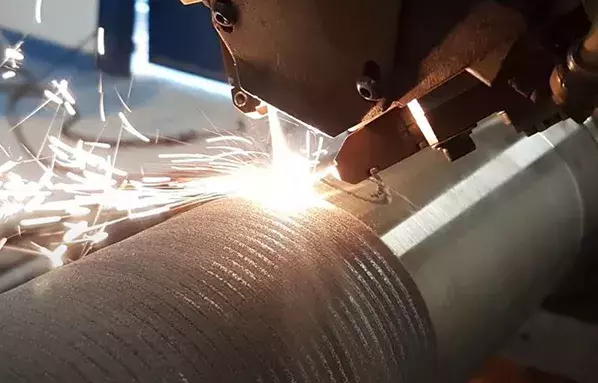
-
Made-to-spec, turnkey offerings | Reman Parts
-
Part inspection | Process selection & qualification | Material selection
-
Technical support | Full-service estimating | Field testing and performance monitoring
-
Pre-cladded LaserClad parts in compliance with OEM specifications
-
Part Reliability Program | Refurbishment and reconditioning of worn components
-
Direct Metal Deposition (DMD) | Hot Wire Cladding (HWC) | Laser ID cladding | Additive Manufacturing
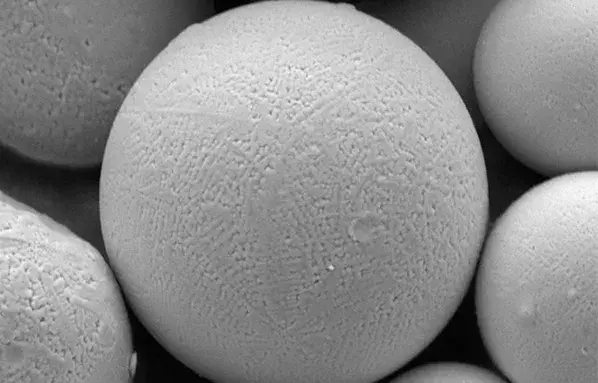
BEST-IN-CLASS LASER CLAD PRODUCTS
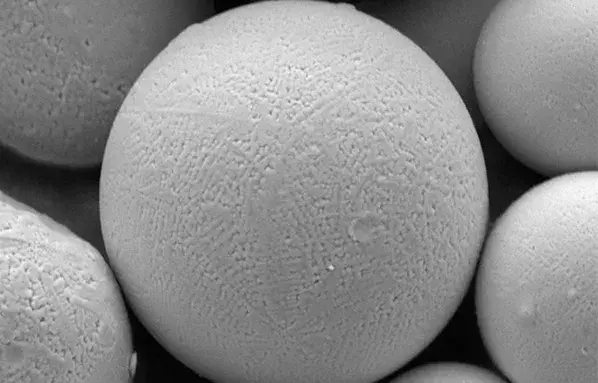
- Reman parts | Chrome plated components
-
Hydraulic parts and components: cylinders, sprocket hub, splitter boxes
-
Bearings, shafts, seals
-
Pump parts: wear rings, shafts, and plungers
-
Compressor rods, rotors, turbine blades
-
Electro motors, fan housings and blades
-
Drilling and downhole equipment
Discover other industries
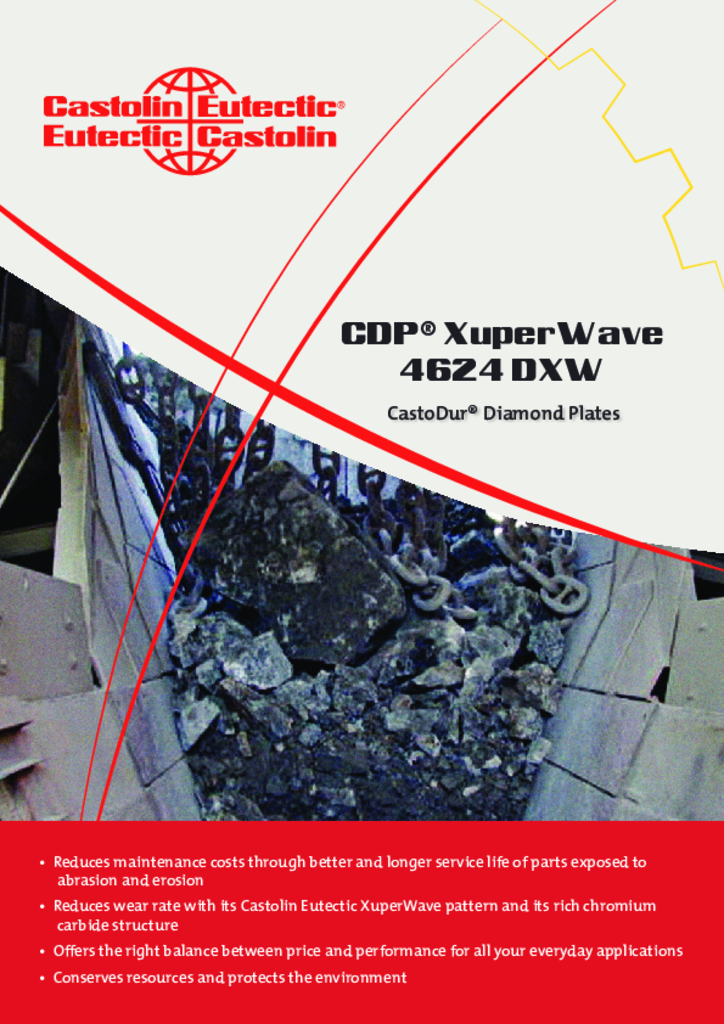
CDP® XuperWave 4624 DXW is the ideal wearplate for the application where the right balance between price and service life is required
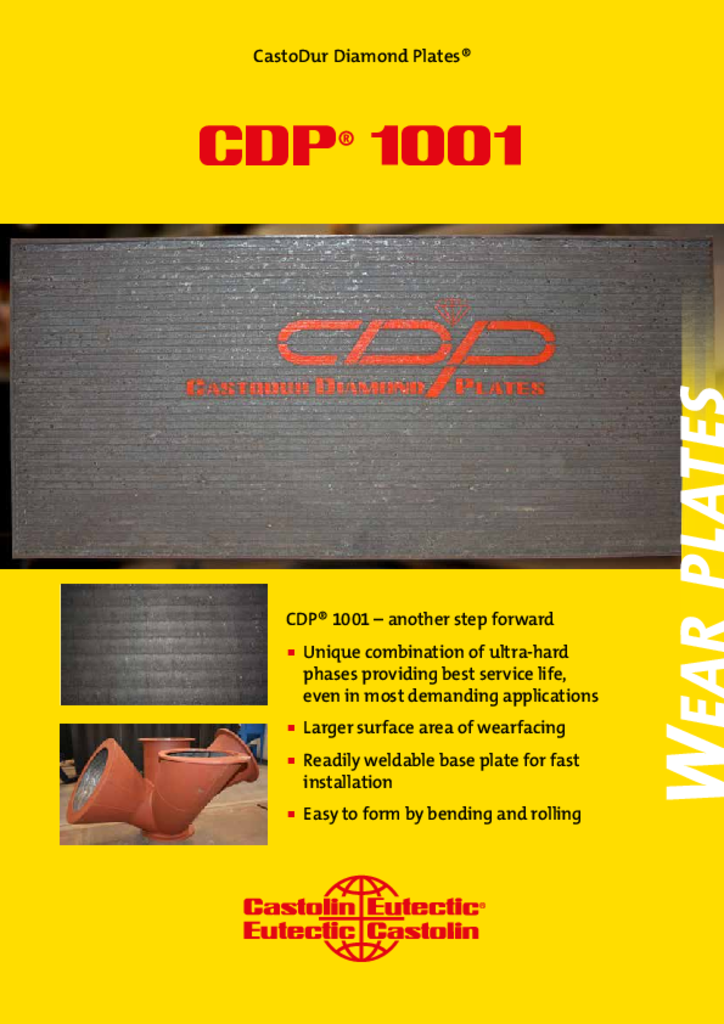
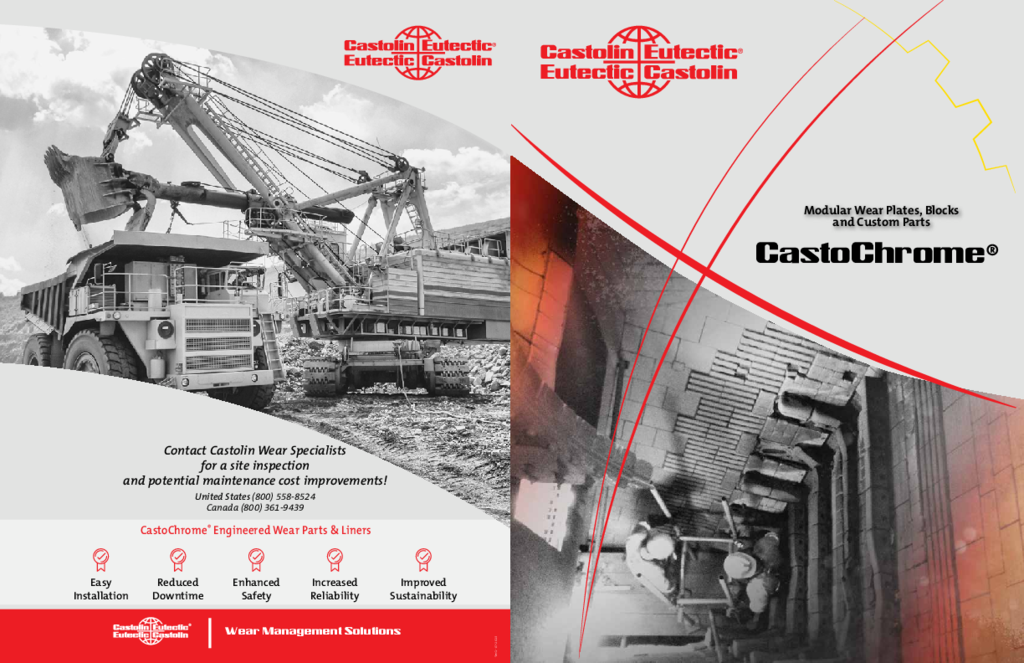