Novel anti-aging solutions for key Steel Industry components
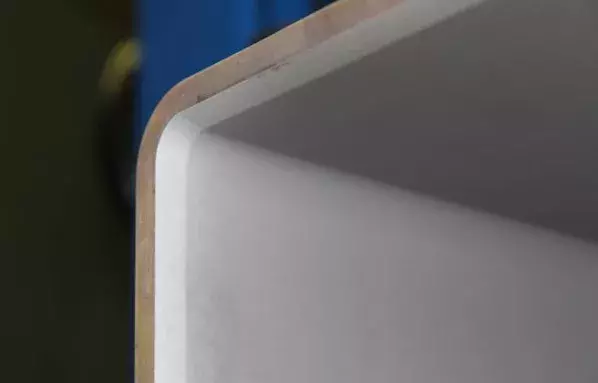
Many steelworks components suffer wear and corrosion due to having to work in hot, corrosive and dust laden environments. Refurbishment with weld overlay rebuild and coating materials are traditional well-establish processes using a range of established alloys and welding procedures. To meet the ever increasing demands to improve performance and cut costs, Castolin Eutectic, a global leader in developing and manufacturing innovative new alloys for welding, thermal spray and laser applications, is continually improving its products and service solutions.
The Castolin Eutectic Group has been involved in the development of wear and corrosion resistant protective coatings for the steel industry since its creation in 1906. Most recently, the acquisition of Monitor Coatings Ltd in the UK has added several new coating solutions for the steel industry.
In continuous casting plants, there is major wear in the copper moulds so the standard nickel coating protection solution has been superseded by advanced ceramic-based, thin thermally sprayed CastCoat coatings applied by HVOF which give 3 to 5 times the wear lifetime. Trials are also underway of a novel XuperCOAT coating for bloom moulds with inner dimensions (square and round) down to 160 mm. The image below compares mould wear of nickel coated and CastCoat moulds based on the practical experience in many plants under conditions of up to 70,000 tonnes cast. Other applications include thin slab caster CSP moulds coated with CastCoat, as well as billet and bloom moulds protected with XuperCoat. The processing parameters must be optimised for each process/alloy couple in order to get the best properties from all these coatings. This is achieved using our own specialist on-site equipment and consumables that are manufactured internally under tight specifications. Our automated systems help to reduce the operational costs while keeping the coating quality to the highest level.
Laser cladding coatings of a NiCrBSi matrix alloy blended with very hard tungsten carbide (WC) particles have shown dramatic life improvements in components used in the transport of steel products in mills and factories. Pulleys, cooling bed rolls, profile rolls (diabolo or similar), roller table rolls, pushing rolls, driving rolls, guiding rolls, spooler rolls, loop lifter rolls. The advent of High Power Diode Laser (HPDL) technology has allowed the previously promising, but expensive laser cladding technology to become a cost effective corrosion solution for large boiler surface areas. This state-of-the-art process allows efficient cladding of steel components in our workshops and competes well against traditional weld overlay while giving better properties such as a lower dilution, a smaller heat affected zone and smooth coating surface and longer lifetimes and thinner coatings. We use laser cladding machines which are coupled with diode lasers up to 8 kW and the high deposition speed and coating thickness flexibility finally allow these excellent coatings to be competitively priced for the steel producers.