New Product
October 3, 2017
New laser cladded sieves offer 10 times higher service life than standard steel
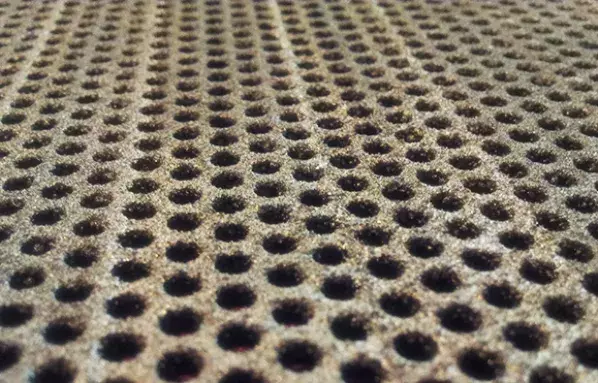
Castolin Eutectic offers now a comprehensive range of LC8 Wear Resistant Sieves with round, square or oval apertures manufactured from 3mm thick or higher, perforated sheets. Our production technology uses a state-of-the-art, high power laser cladding installation. This system ensures highest quality wearfacing coatings of tungsten carbides dispersed in a nickel-based matrix to protect standard perforated steel sheets with variable mesh sizes. The LC8 sieves are currently manufactured at our premises in Vienna, Austria and Incheon, South Korea. We can equally provide tailor-made solutions according to specific customer requests.
The ultra hard tungsten carbide phases which are homogeneously distributed within a self-fluxing, tough nickel-based alloy matrix, provide :
- Extreme wear resistance performance against abrasion and erosion up to 10 times higher than standard, monolithic heat-treated steel alternatives.
- Withstands operating service temperatures up to 400°C. For even higher service temperature requirements, a diverse range of special alloy systems may be proposed to meet specific customer needs.
Five-star Castolin Eutectic LaserCladTM Technology uses a focused laser beam to ensure low heat input welding conditions, which results in extremely effective, wear protective coatings on industrial parts.
Advantages over traditional, hardfacing techniques include :
- Very low dilution which maintains the intrinsic wear resistant properties intact.
- Minimal dissolution of wear resistant tungsten carbide phases into the matrix to improve protective coating performance
- Limited substrate deformation for easy installation and better service life
- Lowest degradation of base metal properties relative to other fusion cladding processes.
Our workshops are fully equipped with laser, plasma and wearfacing welding technologies, water cutting systems, rolling-bending equipment to manufacture tailor-made sieve solutions.
What's new in the Castolin Eutectic world?
Recent Posts