Choose a category
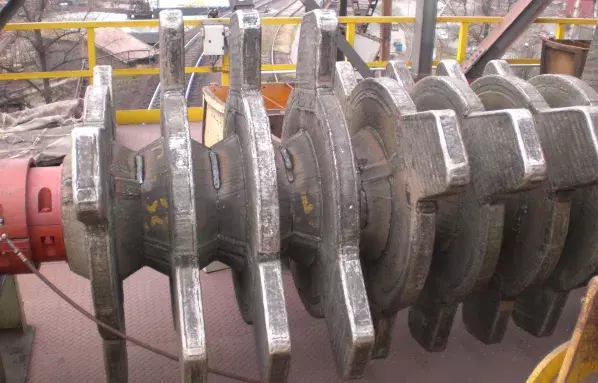
在极端环境下运行
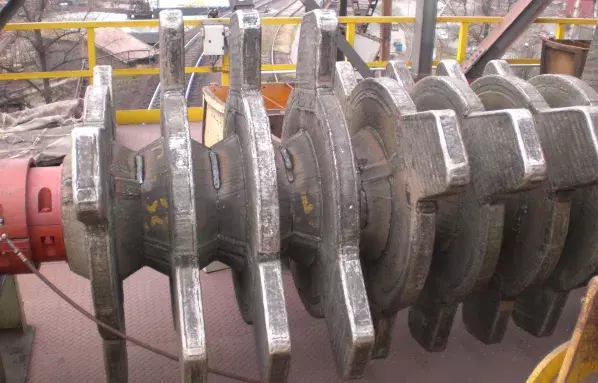
在钢铁厂中,在高温下处理烧结矿的设备会遭受严重的磨损。尤其需要确保对高吞吐量的烧结破碎机提供磨损保护,以避免昂贵的维护费用和频繁的工厂停工。维护负责人普遍认为市场上所提供的标准解决方案不足以满足他们的需求。转子和断路器条必须定期换新。
标准解决方案所提供的耐磨性不足的原因主要有三点:
• 烧结矿的高温降低了耐磨堆焊性能;
• 烧结矿较为粗糙,将磨损部件;
• 高冲击力将对脆性耐磨堆焊造成破坏。
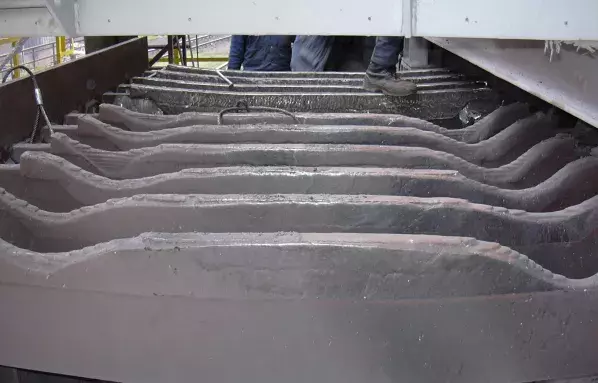
e3 的性能至少比标准解决方案高 3 倍
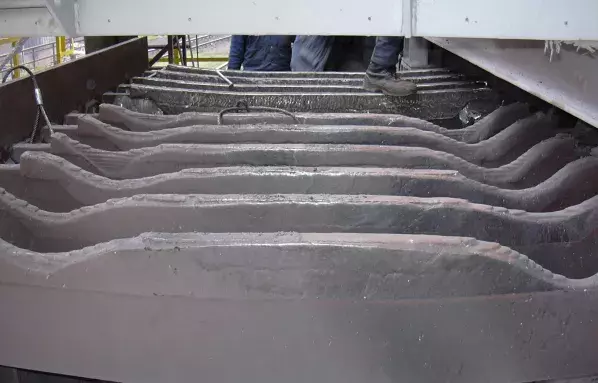
e3 是受法律保护的解决方案,专门为提高钢烧结矿破碎机的生产率并且延长其使用寿命而开发。在实验室以及实际工作条件下经过长达 4 年的测试后,该解决方案终于面世。它基于 Castolin Eutectic 独特的高温耐磨合金制成,即使面对冲击和磨损,也能够提供极高的耐磨性。 e3 尤为适用于保护烧结破碎机的关键零件,例如转盘、齿和破除杆。现场测试表明,e3 的性能至少比标准解决方案高 3 倍。该方案除了能够延长使用寿命外,还保留了部件的几何形状,与标准解决方案相比提高了破碎机效率。
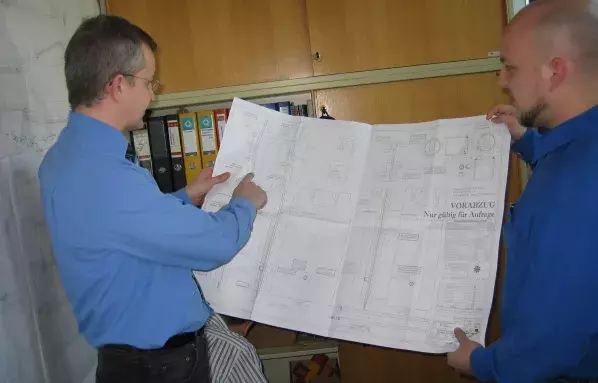
我们的工程师能够根据您的需求,为您打造专有解决方案。
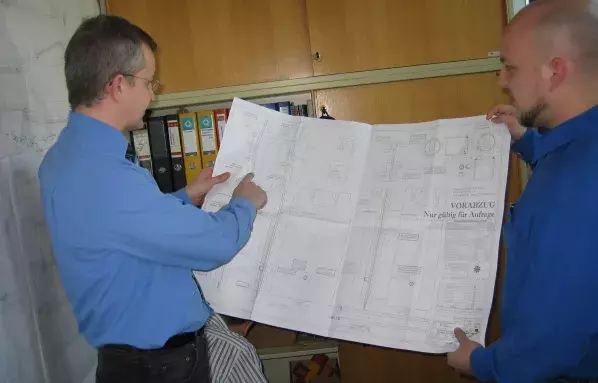
除了延长部件使用寿命之外,e3 还能够:
• 降低烧结矿破碎机的维护频率,减少工厂停工情况的出现;
• 通过保持齿形状以实现更高的破碎机生产效率;
• 减少新部件的采购成本;
• 避免使用复杂的水冷破除杆。
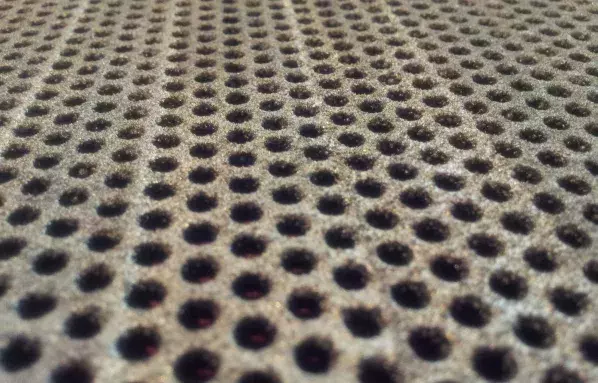
MADE BY LASER CLADDING
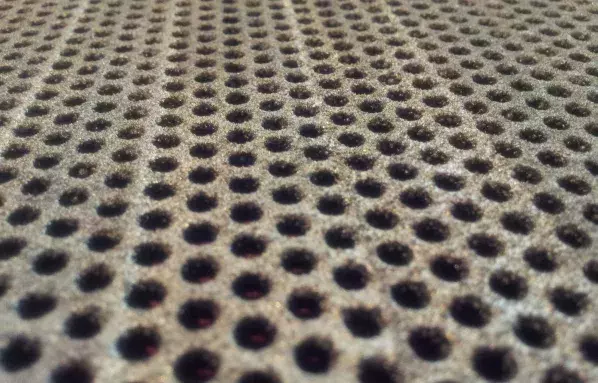
We offer a comprehensive range of wear-resistant sieves with round, square or oval apertures manufactured from 3 mm thick or higher, perforated sheets. We also manufacture tailor-made solutions according to specific customer requests. Our production technology uses a state-of-the-art, high power laser cladding installation. This system ensures highest quality wearfacing coatings of tungsten carbides dispersed in a nickel-based matrix to protect standard perforated steel sheets with variable mesh sizes.
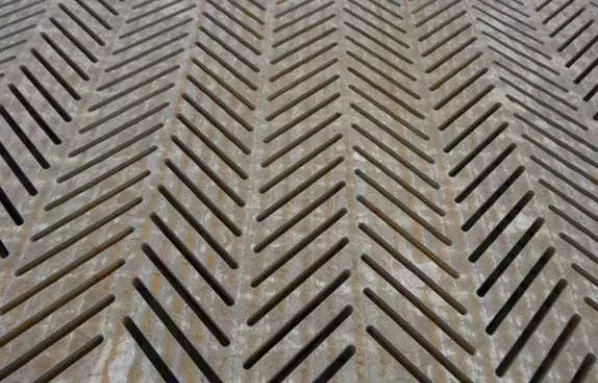
Much better than standard steel
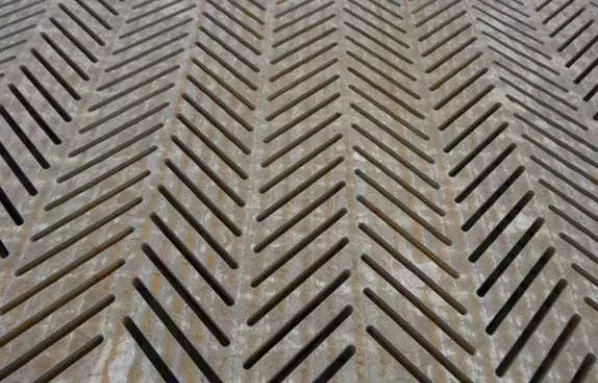
The ultra hard tungsten carbide phases which are homogeneously distributed within a self-fluxing, tough nickel-based alloy matrix, provide:
- Extreme wear resistance performance against abrasion and erosion up to 10 times higher than standard, monolithic heat-treated steel alternatives.
- Withstands operating service temperatures up to 400°C. For even higher service temperature requirements, a diverse range of special alloy systems may be proposed to meet specific customer needs.
Modern Castolin Eutectic LaserClad technology uses a focused laser beam to ensure low heat input welding conditions, which translates into extremely effective, wear protective coatings on industrial parts.
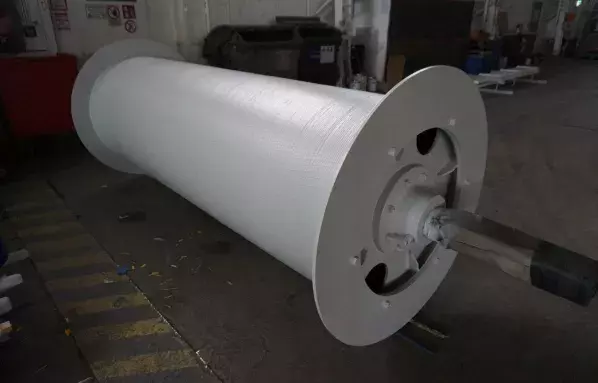
Other Solutions for Sinter Plants
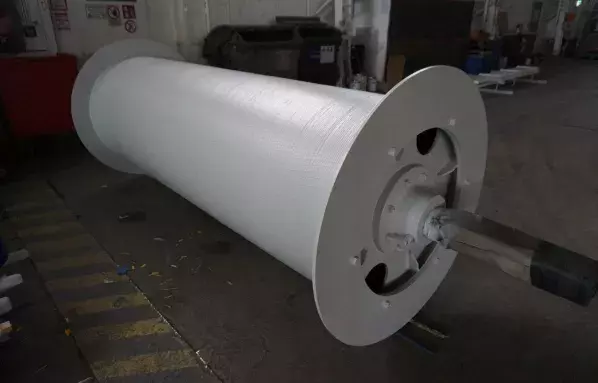
After mixing the raw materials in the sinter plants (fine iron ores, additives such as limestone and olivine, recycled iron-bearing materials from downstream operations, and coke breeze) we find a roller just underneath the charging system to constantly feed the sinter belt which is affected by abrasion. The lifetime of this feeding roller can be increased by our turnkey solutions.
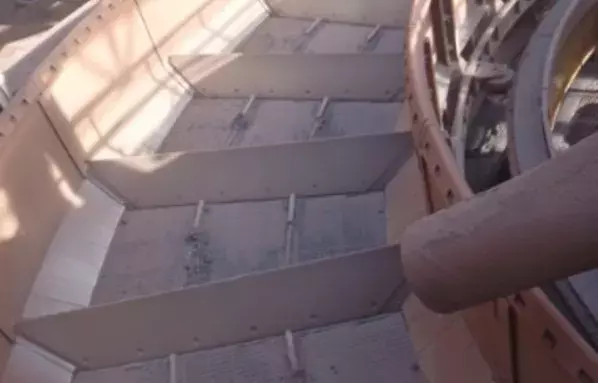
Increase lifetime with CDP® wearplates
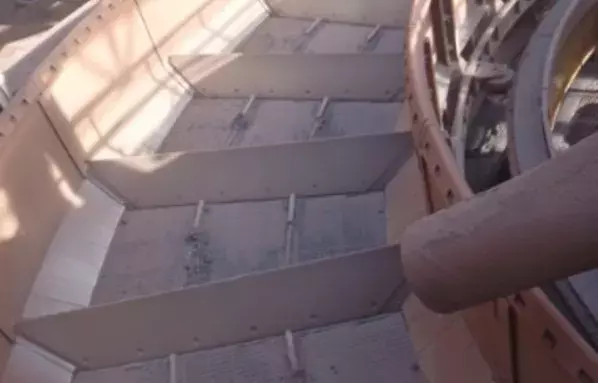
In most cases after the sinter discharge, crushing and hot screening, the sintered material proceeds to a separate cooler. This is typically a rotating structure, divided into circular sectors with tipping devices, in which the sinter is placed in a layer more than 1 m thick and cooled by fresh air.
When the sinter has completed the cooling cycle, each sector is emptied via the tipping device. The cooled sinter is transferred to screens that separate the pieces to be used in the blast furnace.
Both the charge and discharge of the cooler deteriorate the surfaces whose lifetime can be increased with our CDP® wearplates.
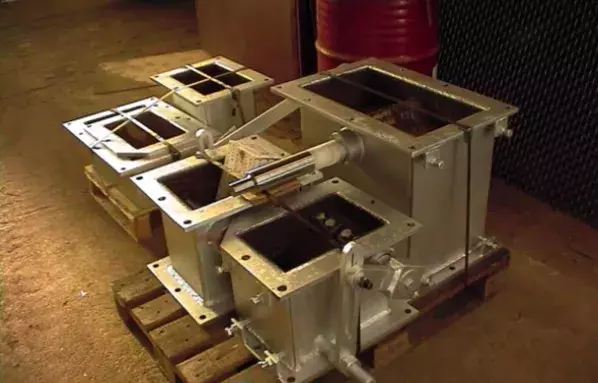
Cooling the steel is a critical factor
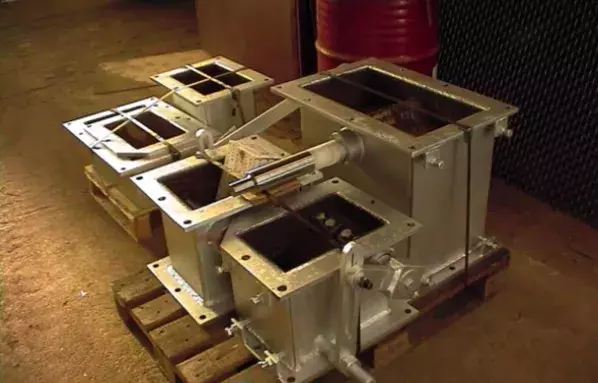
Along the whole sinter process, several metallurgical and chemical reactions take place which produce dust and gaseous emissions apart from the sinter itself. These gases contain particles such as heavy metals that will weaken the inner surface of air suction systems.
A complete high resistance conduction system including valves and transitions circular to square section can be manufactured with our CDP® wearplates.
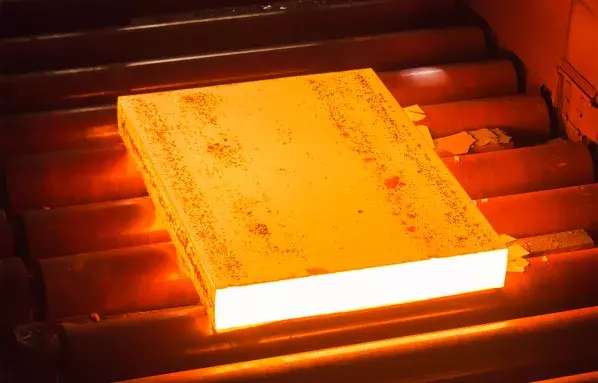
Monitor Coatings 生产的 CastCoat
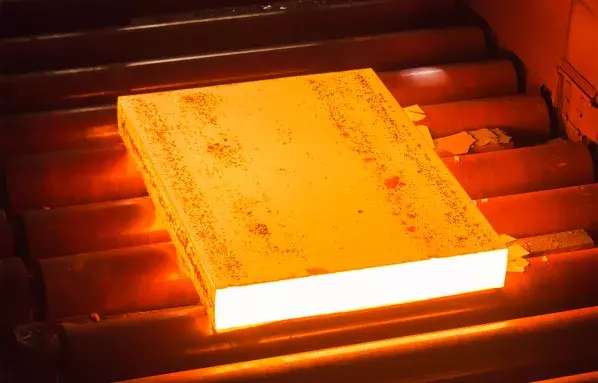
CastCoat 硬质复合涂层是由 Castolin Eutectic 在英国的子公司 Monitor Coatings 开发,该涂层可用于钢铁行业,尤其是作为连铸机铜模具板的涂层。该涂层自投入使用以来,至今已有 20 多年的历史。测试表明,该涂层比任何其他可用的铜模板涂层都更为坚硬。该涂层的摩擦系数很低,有助于减少摩擦警报,并且其对液态钢和铸造粉末呈惰性。涂层系统对模具液位检测器或电磁搅拌器没有影响。此外,经证明该涂层对传热速率的影响可忽略不计。
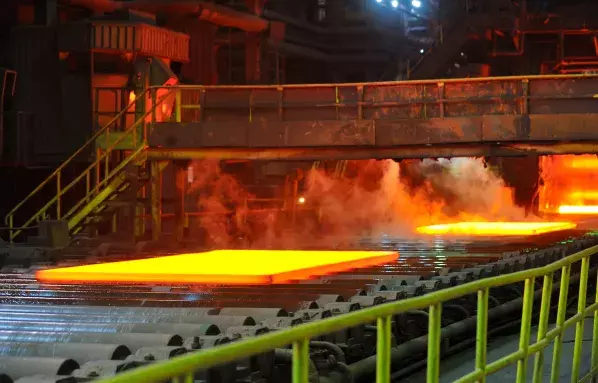
现已成长为一项成熟的技术
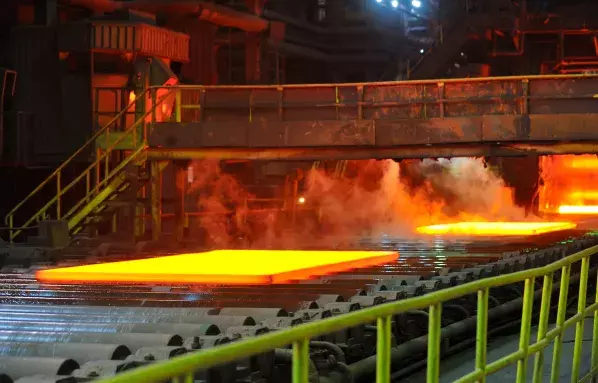
结合多年以来所收集的涂层相关的现场数据,可以发现铜板寿命出现显著延长:厚板坯连铸机的寿命延长了 3-4 倍,薄板坯连铸机窄板的寿命延长了 6 倍,并且还改善了产品的形状。在操作过程中,已证明该涂层能够通过显著提高耐磨性来延长铸造使用时间。由于高应力状态下的热疲劳,最终导致了涂层的逐步降解。如今,CastCoat 已成长为一项成熟的技术,在全球范围内拥有广泛的客户基础,始终如一地为用户降低每吨成本。
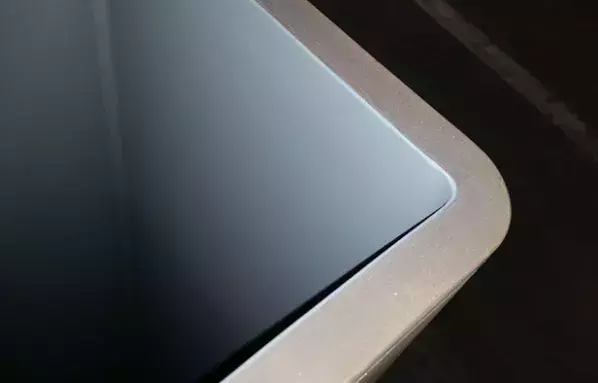
新型紧凑型 HVOF 设备
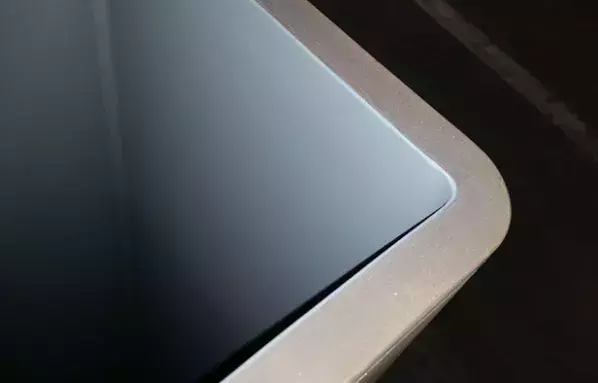
通过对模具的全部四个面进行涂覆,在整个加工过程中保持了模具尺寸稳定性,从而实现持续有效的产品形状和坯壳生长。缺乏明显的磨损意味着在模具更换期间可维持更久的作业,从而实现更高的连铸机利用率。此外,涂层提供的保护可延长铜板的使用寿命,从而可以节省铜,并显著降低在线和离线维护成本。利用紧凑型 HVOF 设备的最新发展,CastCoat 复合涂层现在可以在管模上应用。
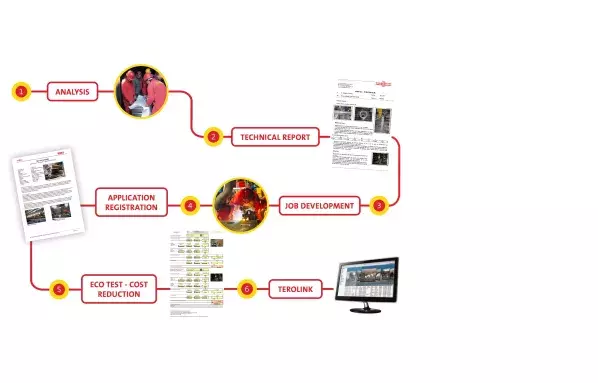
Our working method for cost savings
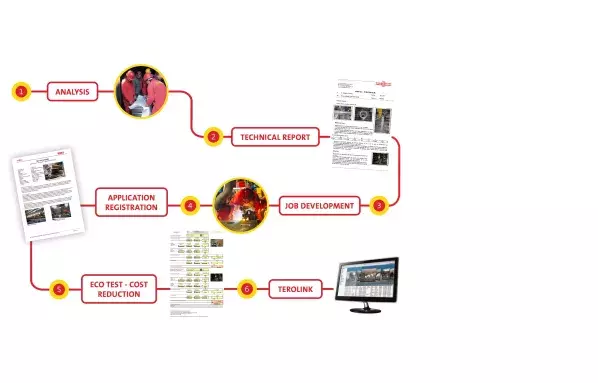
Since a very long time we are successfully applying a partnership program, focused on cost reductions. This smart Maintenance and Repair program can be summarized in six steps:
- Analysis: The first step to a good solution is a correct analysis.
- Technical Report: With the information provided, our Technical Department prepares a report.
- Job development: Once the client considers the repair to be feasible, Castolin Eutectic puts at your service all the Technical Department for the development of the procedure outlined above.
- App registration: Always subject to the customer’s approval, we first propose to register the job done in our confidential “FAR” database where the short application summary remains on hold until confirmation of service results.
- EcoTest: At the end of the service life of the part involved, we are ready to establish a detailed cost analysis to evaluate the practical direct savings achieved through mutual collaboration.
- Terolink: Finally we propose to submit the complete application as verified in our Terolink Database.
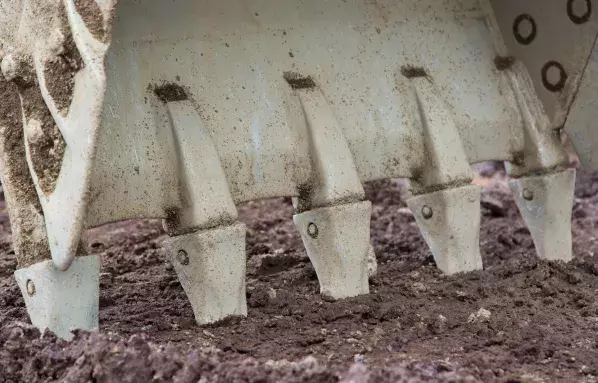
RAW MATERIAL PROCESSING & HANDLING
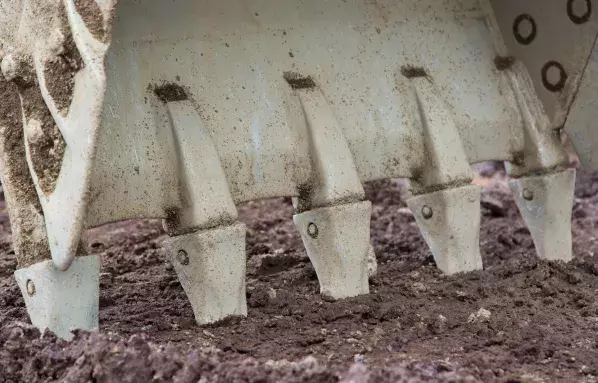
Iron ore, coal, limestone, fluxes and scrap are unloaded in the raw material area. They are classified, stored, crushed, grinded and handled for transport into the next production process. All these activities produce a combination of wear phenomena in the different machines and parts involved. Their service lifetime can be extended with different solutions, thanks to the cost reduction program from Castolin Eutectic.
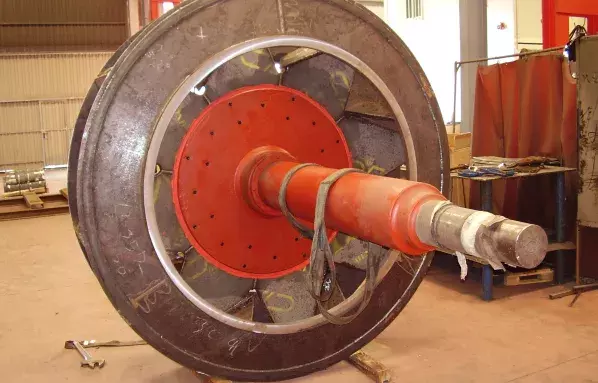
The first step for a good solution is a correct analysis
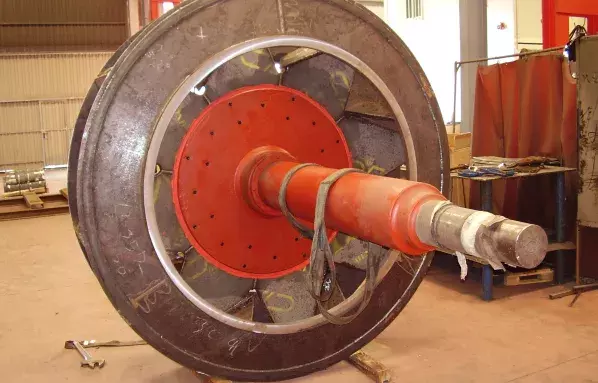
After processing the respective raw materials, they pass through the blast furnace, electric arc furnace (EAF) or basic oxygen furnace (BOF) to get pig iron or Steel. The first step for a good solution is a correct analysis. To facilitate this, we have created an analysis document that can easily be completed in collaboration with our technical delegate. The document reflects the most important parameters to be considered to develop in-house solutions to your wear problems.
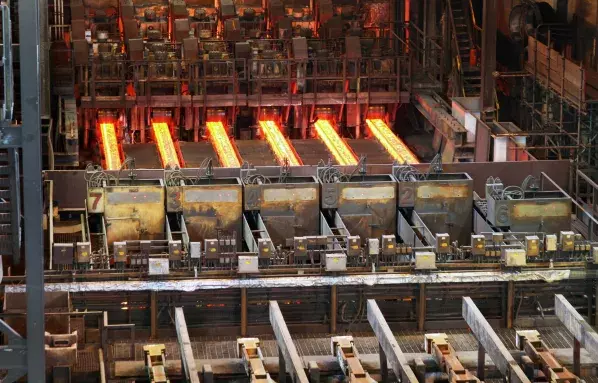
Repair Continous Casting Rollers according to OEM specifications
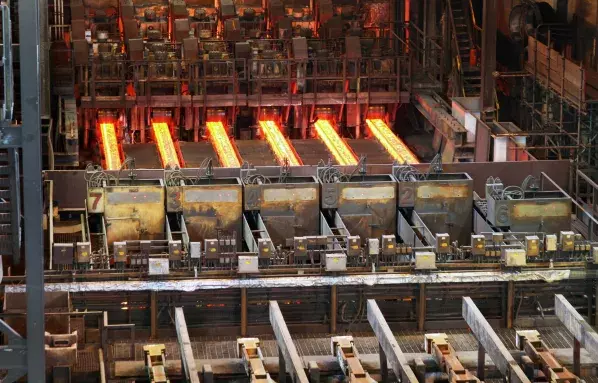
Continuous casting rolls are critical parts that are used for making the slabs, blooms or billets just after the tundish and moulds, at a very high temperature. The extreme working loads as well as the high temperature wear-out the rolls surface and, as a result, parts are damaged. Maintenance managers regularly have to decide to either scrap these expensive parts or try to repair them according to OEM specifications.
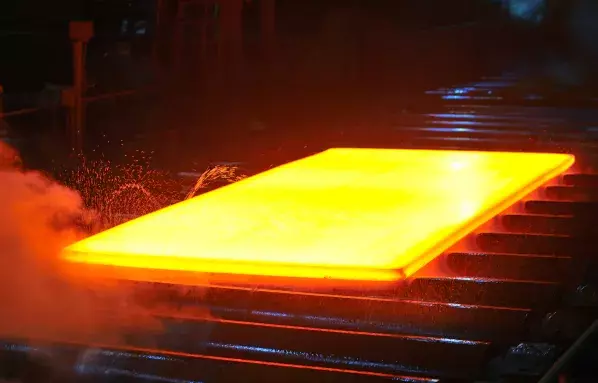
Rebuilding and repairing rolls for steel processing facilities
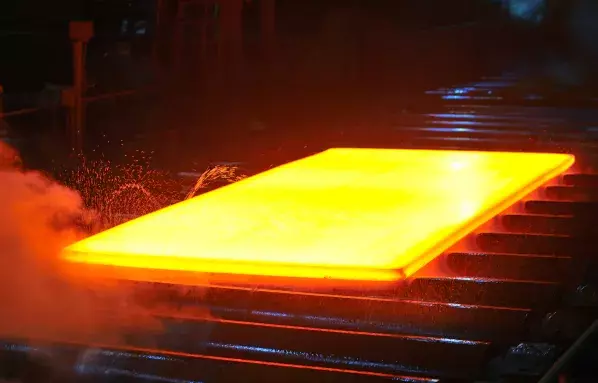
The semifinished products obtained after the continuous casting process have to be shaped before being comercialized. The first of these processes is hot rolling, from which sometimes final products are obtained and other times semifinished products intended for cold rolling or coating.
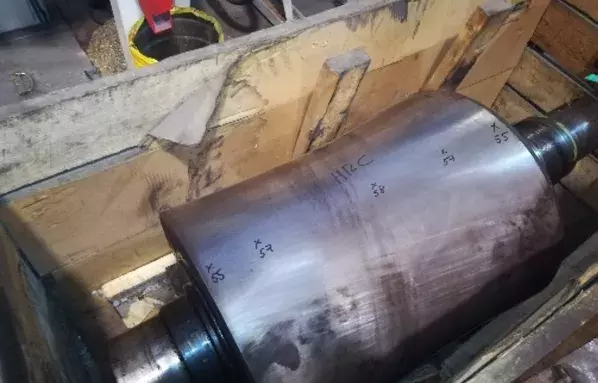
cooling the steel is a critical factor
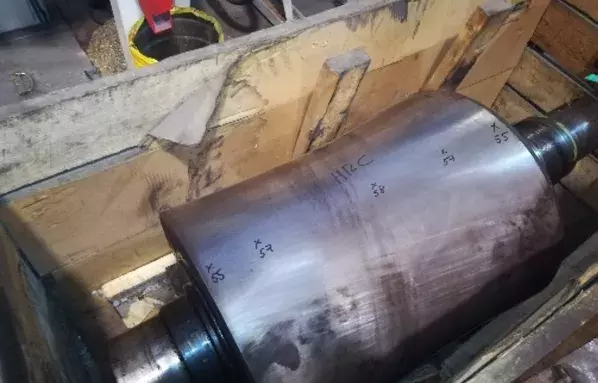
In all rolling processes, cooling the steel is a critical factor. The speed at which the rolled product is cooled will affect the mechanical properties of the steel. Cooling speed is controlled normally by spraying water on the steel as it passes through and/or leaves the mill, although occasionally the rolled steel is air-cooled using large fans.
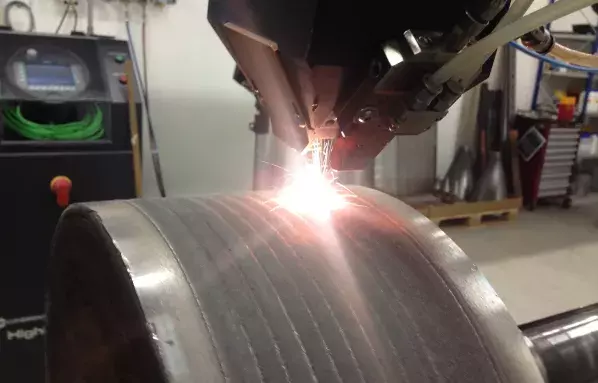
Rolls protected by laser cladding
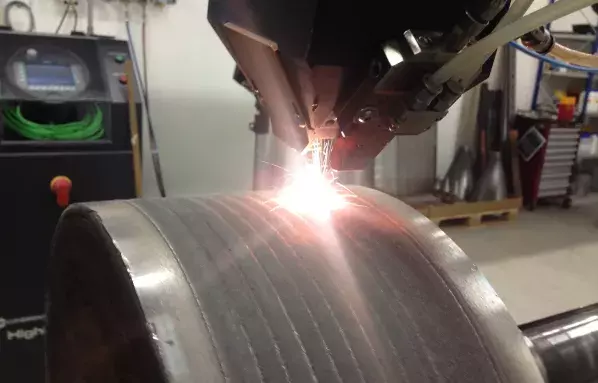
Since the installation of laser cladding technology in the Castolin Eutectic Services Centers the wear protection of key tools such as rolls and guides has been raised to a new level. The utilization of 8kW High Power Direct Diode (HPDD) with automation leads to flexible production and superior quality. In addition, the powerful laser enables high deposition rates that can reduce the cost of the cladding operation. Compared to standard welding techniques, the dissolution of the carbides and the dilution of the cladding material are the lowest that can be achieved. As a result, the wear-resistance is maximized and the service-life is longer. The unique broad beam (up to 23mm wide) produces a flat coated surface that minimizes subsequent machining or grinding. Rolls can often be used as welded without further processing. The low heat input of the laser process means the lowest distortion of large and thin wall parts that can easily be cladded.
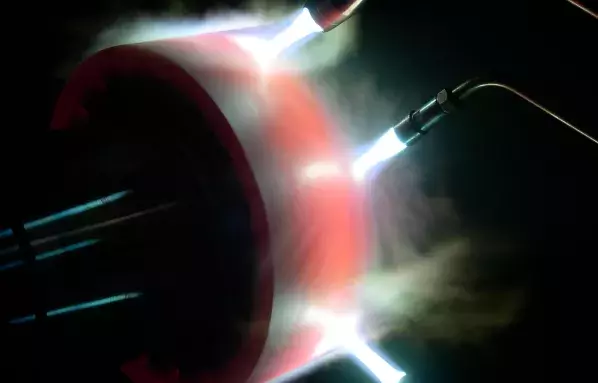
Rolls protected by spray & fuse
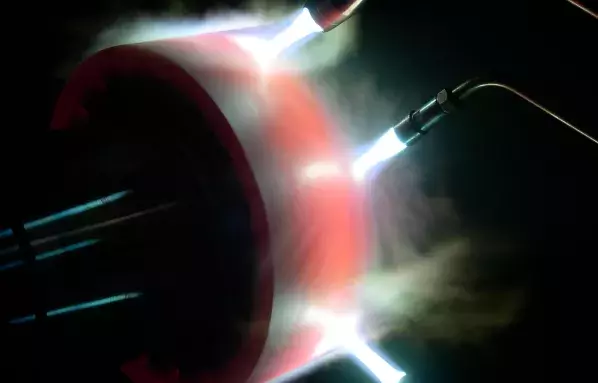
OEMs usually provide parts that have the surface coated with high wear resistant alloys such as Eutalloy® RW 12496. This coating is applied first by spraying a powder on the roller surface and then by fusing it just above the liquidus temperature. The process allows the coating to offer its best wear resistant properties and to perfectly bound on the steel substrate. On long and heavy parts, fusion is extremely difficult to be done correctly. Just after the spraying step, the part must be pre-heated homogeneously and kept in temperature while several torches fuse the powder all along the roll. In 2m long massive rolls, fusion may require up to 7 hours and any variation in temperature may result on an irregular surface quality. Since the part is exposed to very high temperature, deformation is also critical, especially on rolls made with thin wall tubes. Finally, if cooling is not well managed, thermal stresses can be so high that cracks may appear on the overlay. Our well-equipped service workshops as well as more than 10-years experience allow us to offer high quality overlays. Parts are coated by highly skilled operators that follow strict manufacturing methods. They regularly apply several powders according to what has been defined by OEMs.
发现其他行业
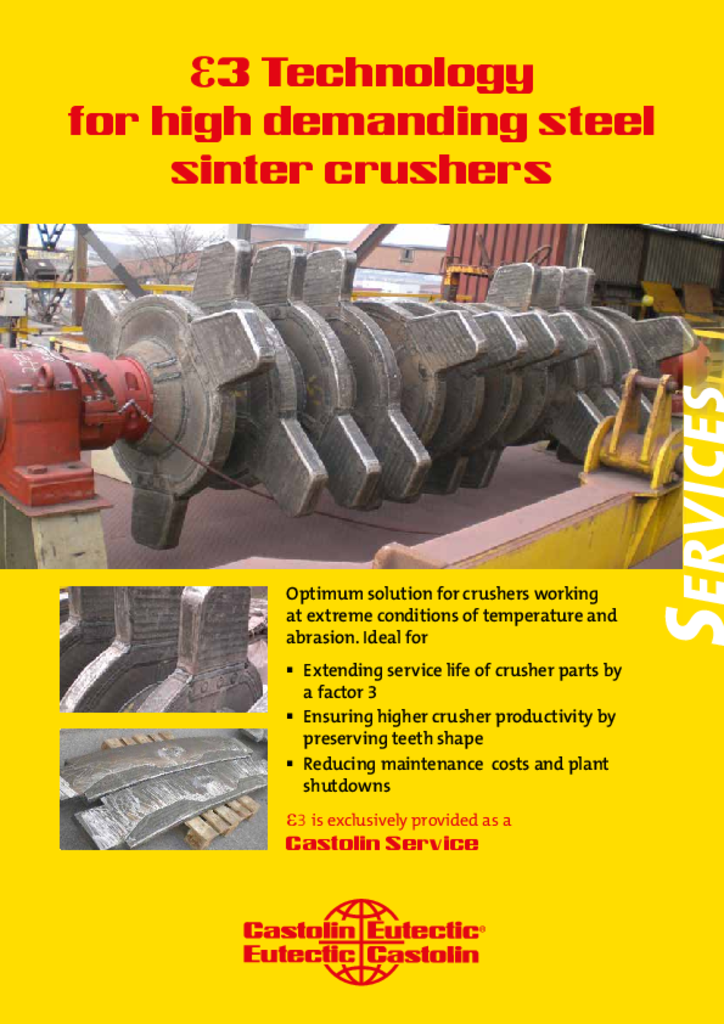
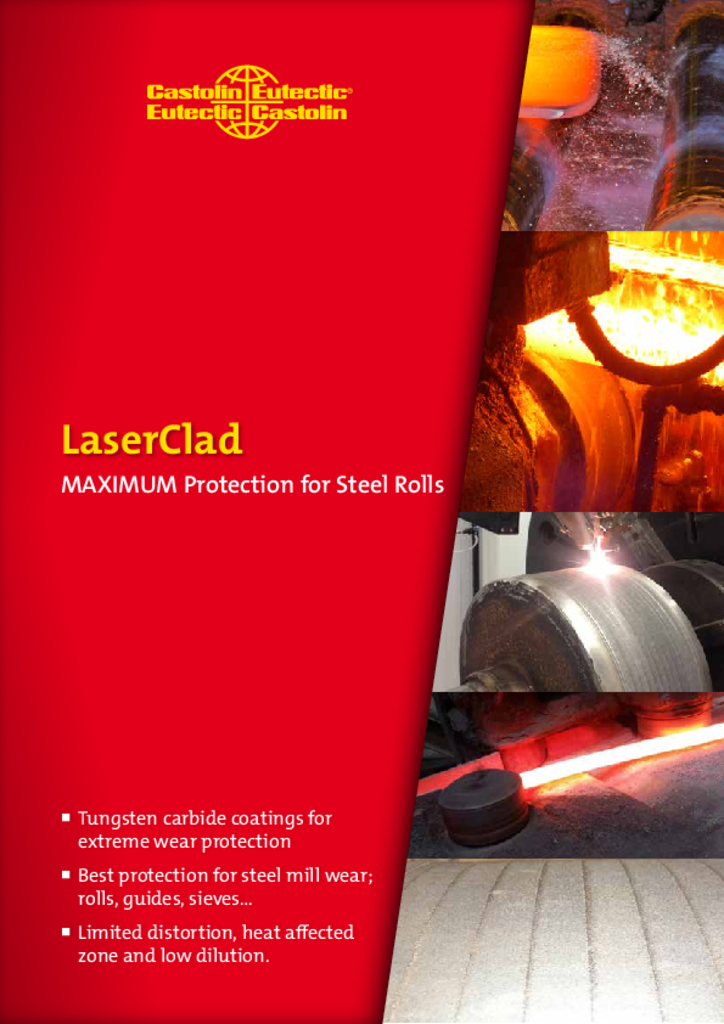
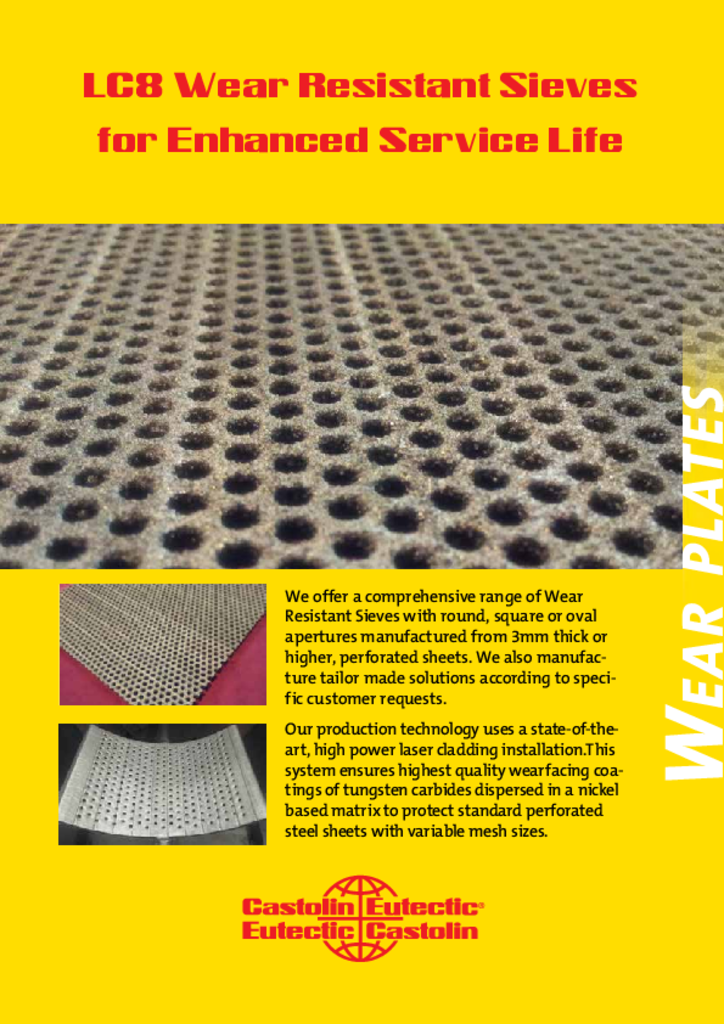