Teräs
Choose a category
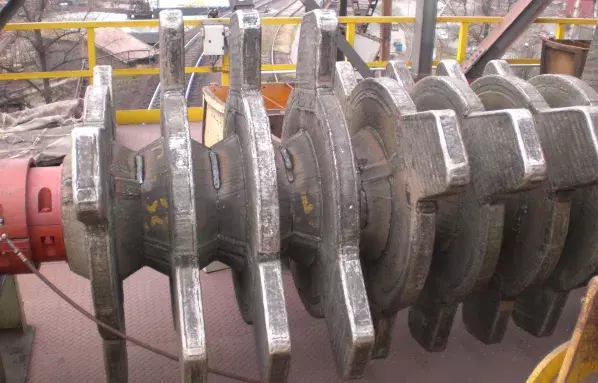
Operating in extreme environments
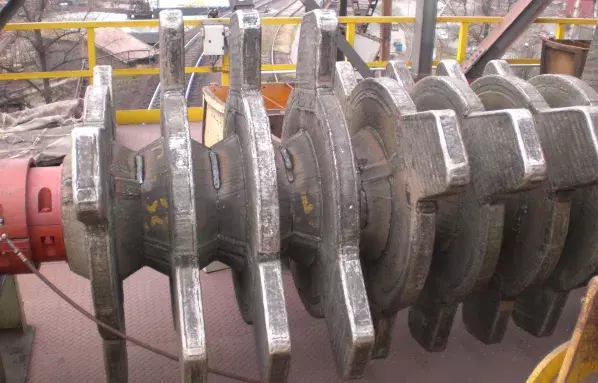
In steel plants, equipment that processes sinter at very high temperature is exposed to severe wear conditions. In particular, the sinter crusher that has to ensure large through-put must be wear-protected in order to avoid expensive maintenance and frequent plant shutdowns. Maintenance Managers agree that standard solutions available on the market are not sufficient for their needs. Rotors and breaker bars must regularly be replaced with new ones.
The insufficient wear resistance of the standard solutions is due to three main factors:
• the sinter high temperature that reduces the hardfacing characteristics,
• the sinter abrasive nature that wears-out the parts,
• the high impacts that destroy brittle hardfacings.
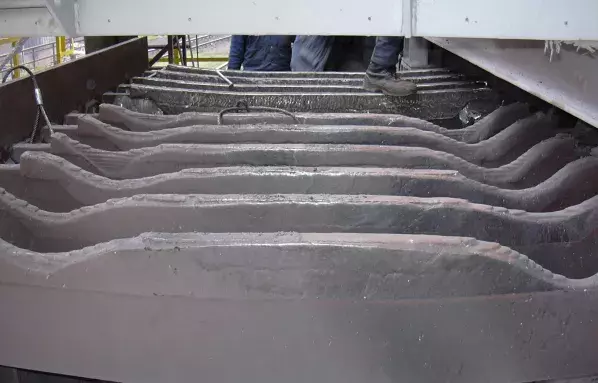
Outperforms standard solutions by at least a factor 3
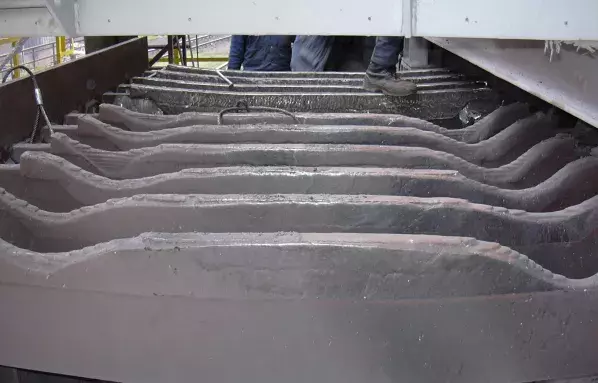
e3 is a legally protected solution specifically developed for improving steel sinter crusher productivity and service life. This solution is born after 4 years of tests made in laboratory as well as on real working conditions. It is based on a unique Castolin Eutectic high temperature wear-resistant alloy that offers extreme resistance even when impact and abrasion are present. e3 is particularly suitable for protecting the critical sinter crusher parts such as the rotor discs, teeth and breaker bars. On-site tests have shown that e3 outperforms standard solutions by at least a factor 3. In addition to increasing service life, the geometrical shape of the parts is preserved, which ensures better crusher efficiency compared to standard solutions.
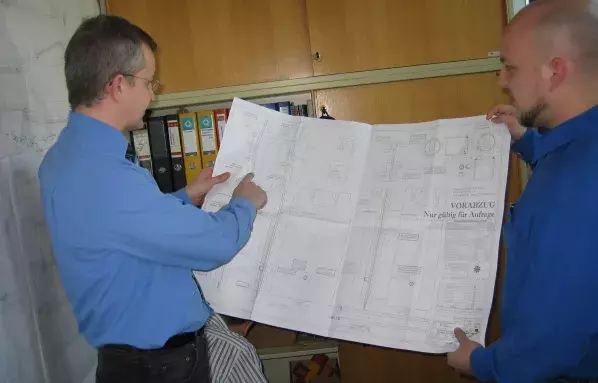
Our engineers can design a specific solution for your own needs
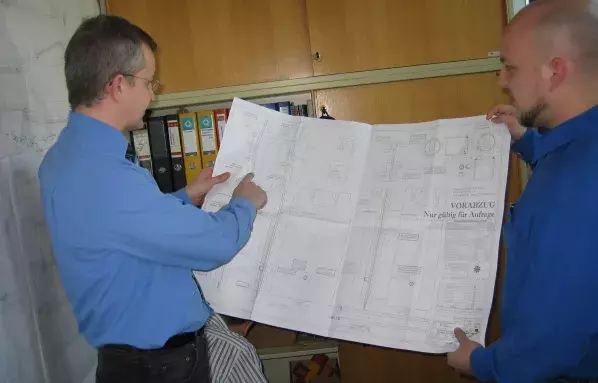
In addition to boosting part service life, e3 allows you:
• to reduce frequent sinter crusher maintenance and plant shutdowns,
• to get higher crusher productivity by preserving teeth shape,
• to reduce purchasing costs of new parts,
• to avoid using complex water-cooled breaker bars.
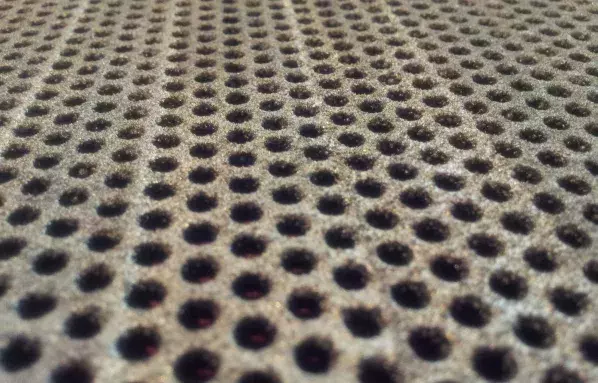
MADE BY LASER CLADDING
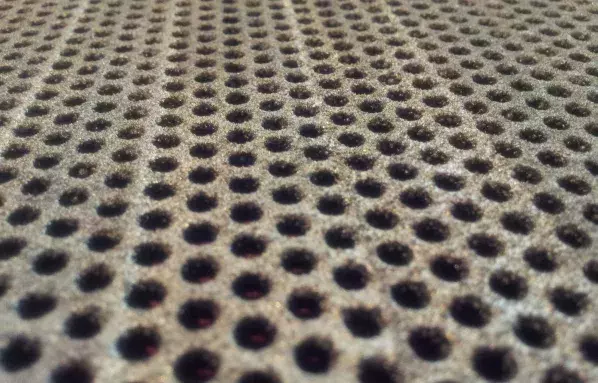
We offer a comprehensive range of wear-resistant sieves with round, square or oval apertures manufactured from 3 mm thick or higher, perforated sheets. We also manufacture tailor-made solutions according to specific customer requests. Our production technology uses a state-of-the-art, high power laser cladding installation. This system ensures highest quality wearfacing coatings of tungsten carbides dispersed in a nickel-based matrix to protect standard perforated steel sheets with variable mesh sizes.
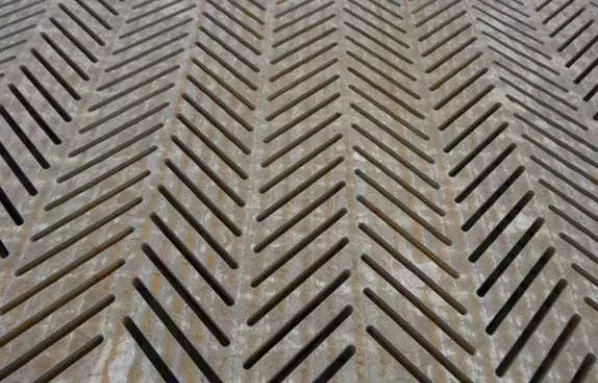
Much better than standard steel
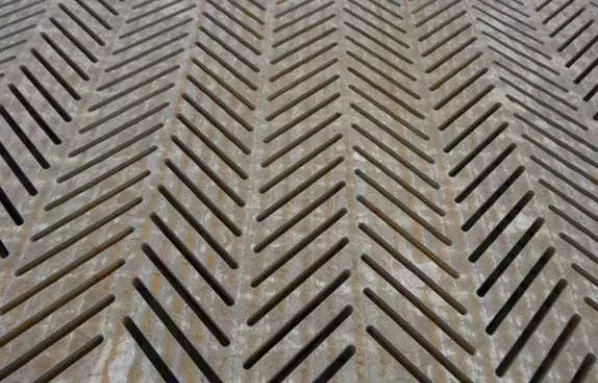
The ultra hard tungsten carbide phases which are homogeneously distributed within a self-fluxing, tough nickel-based alloy matrix, provide:
- Extreme wear resistance performance against abrasion and erosion up to 10 times higher than standard, monolithic heat-treated steel alternatives.
- Withstands operating service temperatures up to 400°C. For even higher service temperature requirements, a diverse range of special alloy systems may be proposed to meet specific customer needs.
Modern Castolin Eutectic LaserClad technology uses a focused laser beam to ensure low heat input welding conditions, which translates into extremely effective, wear protective coatings on industrial parts.
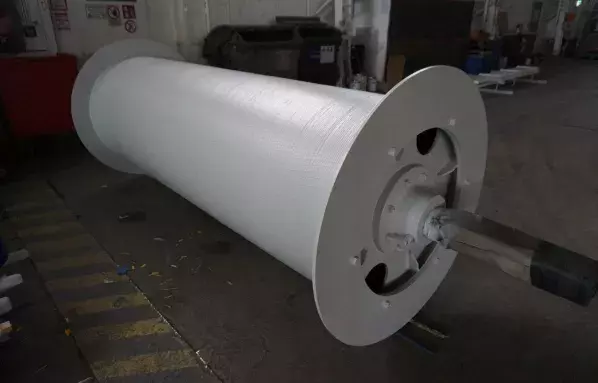
Other Solutions for Sinter Plants
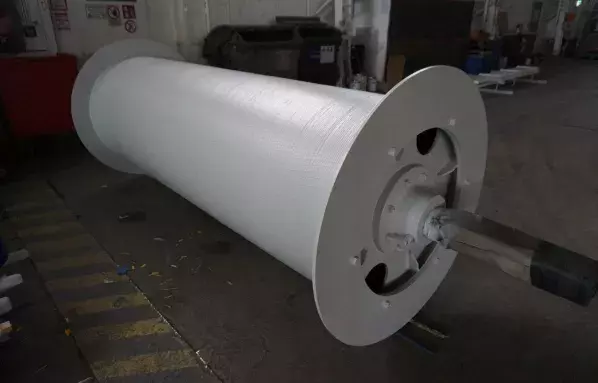
After mixing the raw materials in the sinter plants (fine iron ores, additives such as limestone and olivine, recycled iron-bearing materials from downstream operations, and coke breeze) we find a roller just underneath the charging system to constantly feed the sinter belt which is affected by abrasion. The lifetime of this feeding roller can be increased by our turnkey solutions.
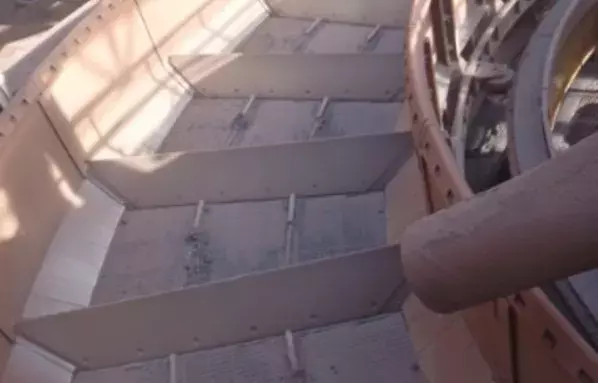
Increase lifetime with CDP® wearplates
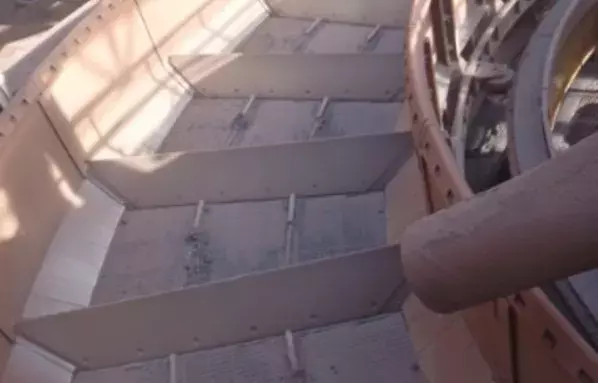
In most cases after the sinter discharge, crushing and hot screening, the sintered material proceeds to a separate cooler. This is typically a rotating structure, divided into circular sectors with tipping devices, in which the sinter is placed in a layer more than 1 m thick and cooled by fresh air.
When the sinter has completed the cooling cycle, each sector is emptied via the tipping device. The cooled sinter is transferred to screens that separate the pieces to be used in the blast furnace.
Both the charge and discharge of the cooler deteriorate the surfaces whose lifetime can be increased with our CDP® wearplates.
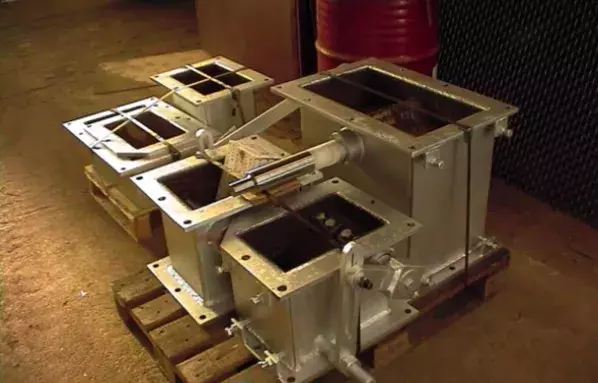
Cooling the steel is a critical factor
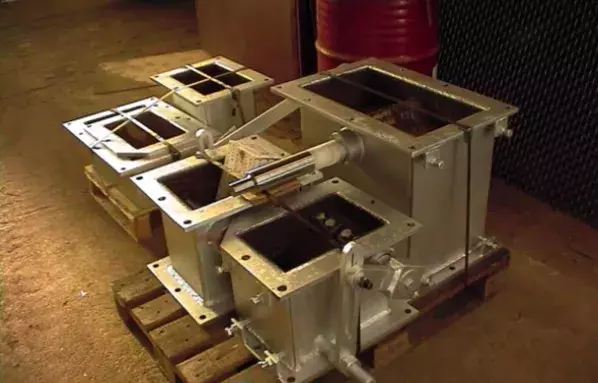
Along the whole sinter process, several metallurgical and chemical reactions take place which produce dust and gaseous emissions apart from the sinter itself. These gases contain particles such as heavy metals that will weaken the inner surface of air suction systems.
A complete high resistance conduction system including valves and transitions circular to square section can be manufactured with our CDP® wearplates.
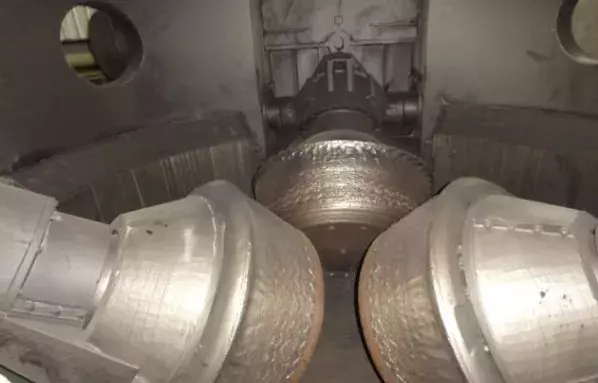
Preventive wear protection of VRMs
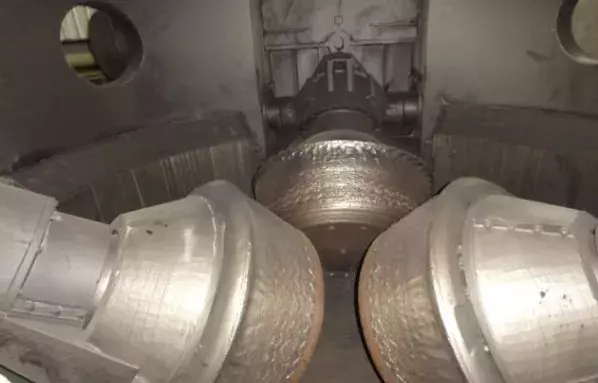
Based upon hundreds of successful applications approved by our clients across the globe, Castolin Eutectic can provide optimized solutions with a wide range of products and technologies to combat wear in VRM (Vertical Roller Mill) and many more. Castolin Eutectic has a detailed understanding of the industries where this equipment is used, of every major wear problem and can provide industry tested application solutions.
From the extreme cold of Russia to the heat of Brazil and Mexico, we have a deep knowledge of application solutions for the wear problems in this industry. Innovative technologies and equipment help major industrial Groups to meet their objectives in terms of increased life time and plant performance.
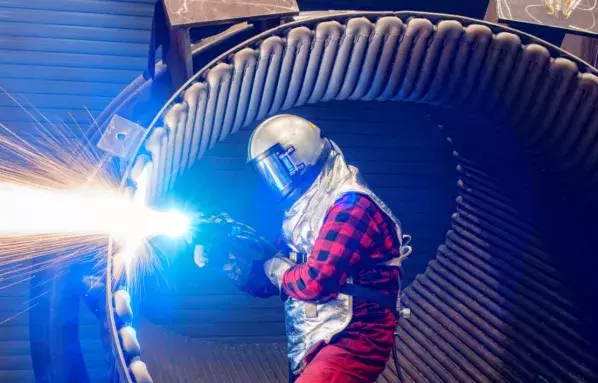
Limited distorsion or shrinkage
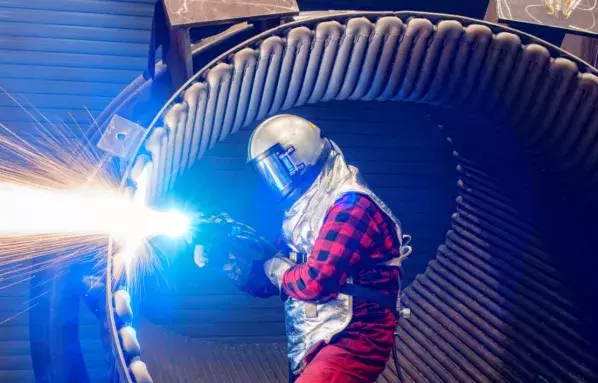
The fume ducts in the Steel Plants are exposed to high erosion wear or corrosion. Moreover, their internal walls are subjected to the impact of erosive particles transported at high speed by ventilation gas at high temperatures. In some applications, ventilation gas is also corrosive.
Since decades, Castolin Eutectic has been the provider of choice for service, repair and preventive maintenance of heavy-duty and industrial process equipment.
In Iron & Steel, protecting your industrial process equipment, fume ducts, tubes and walls from future corrosion and erosion while also extending your tubes’ useful life, is vital to your operation’s bottom line.
Eutronic Arc is the highest productivity and lowest running cost thermal spraying process. Due to the low heat input, there is a very low dilution during the process with limited distortion or metallurgical modification of the substrate without any dilution.
This technology can be applied both in the workshop or in the field. It does not require the use of oxygen, kerosene or combustible gas which means more economic coatings.
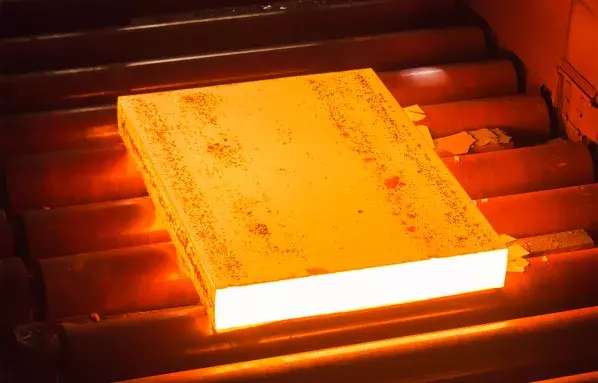
CastCoat from Castolin Eutectic
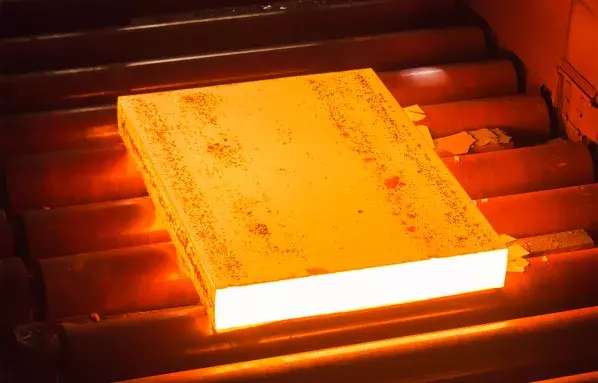
The CastCoat hard composite coating was developed by the advanced Castolin Eutectic workshop in Newcastle, UK, for steel industry applications in particular for coating continuous Caster copper mould plates, for more than 20 years. Tests have shown that the coating is tougher than any other copper mould plate coating available. It has a low coefficient of friction which helps reduce sticker alarms and the coating is inert to liquid steel and casting powders. The coating system has no effect on mould level detectors or electromagnetic stirrers. It has also been proven that the coating has negligible effect on heat transfer rates.
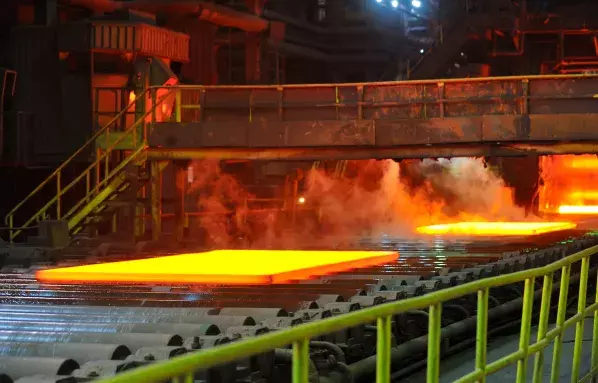
Now a mature technology
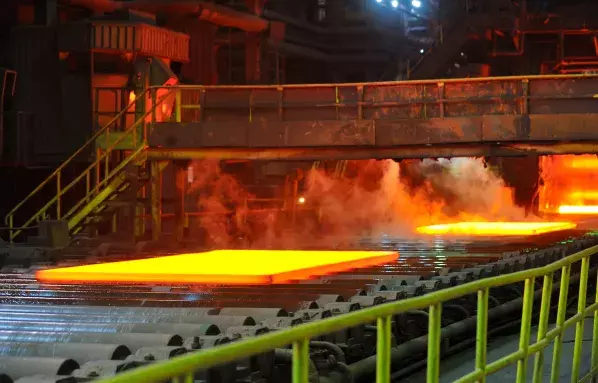
With years of field data behind the coating, significant copper plate life improvements have been demonstrated: 3 – 4 times for thick slab casters and up to 6 times for thin slab caster narrow plates, accompanied by improved product shape. In operation, the coating has been shown to enable extended casting runs through dramatic increases in wear resistance. Eventual progressive degradation of the coating occurs due to the thermal fatigue in high stress positions. Now a mature technology with a worldwide customer base, CastCoat continues to provide users with reduced costs/tonne.
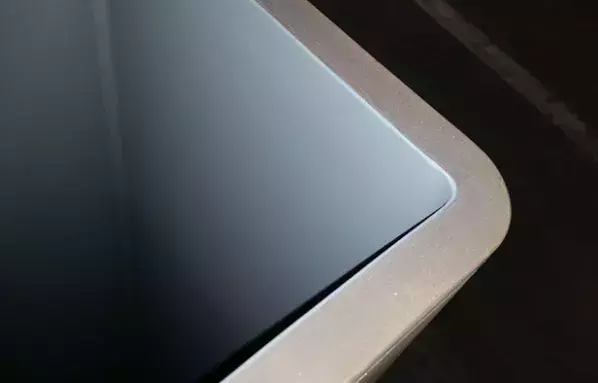
New compact HVOF device
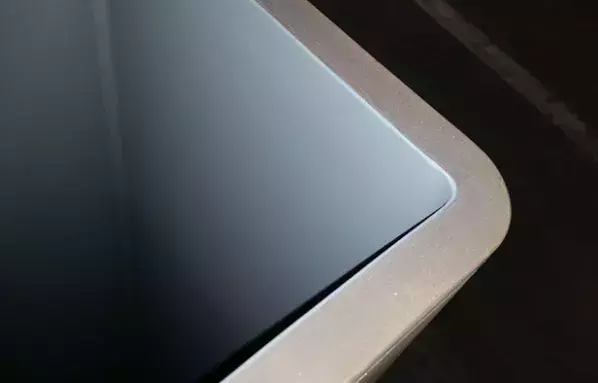
By coating all four faces of the mould, dimensional stability is retained throughout the campaign, leading to sustained and effective product shape and shell growth. The lack of appreciable wear means longer campaigns are possible between mould exchanges, achieving higher caster availability. In addition, the protection offered by the coating gives extended copper plate life, resulting in annual copper savings and delivering significant reductions in both on and off-line maintenance costs. With the recent development of a compact HVOF device, the CastCoat Composite Coating can now be applied to tube moulds.
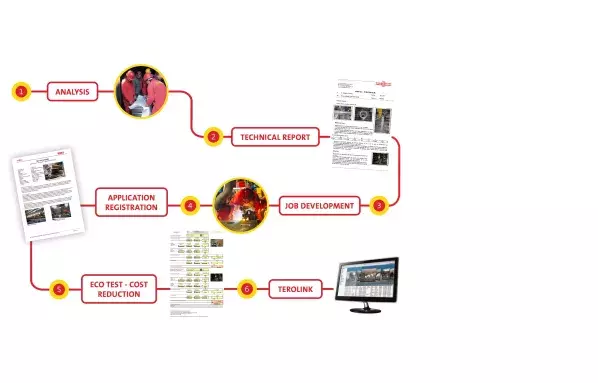
Our working method for cost savings
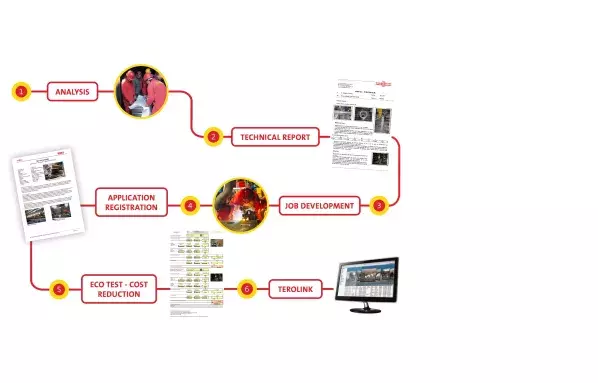
Since a very long time we are successfully applying a partnership program, focused on cost reductions. This smart Maintenance and Repair program can be summarized in six steps:
- Analysis: The first step to a good solution is a correct analysis.
- Technical Report: With the information provided, our Technical Department prepares a report.
- Job development: Once the client considers the repair to be feasible, Castolin Eutectic puts at your service all the Technical Department for the development of the procedure outlined above.
- App registration: Always subject to the customer’s approval, we first propose to register the job done in our confidential “FAR” database where the short application summary remains on hold until confirmation of service results.
- EcoTest: At the end of the service life of the part involved, we are ready to establish a detailed cost analysis to evaluate the practical direct savings achieved through mutual collaboration.
- Terolink: Finally we propose to submit the complete application as verified in our Terolink Database.
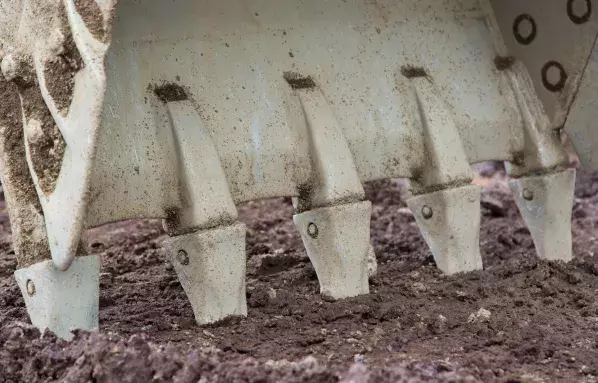
RAW MATERIAL PROCESSING & HANDLING
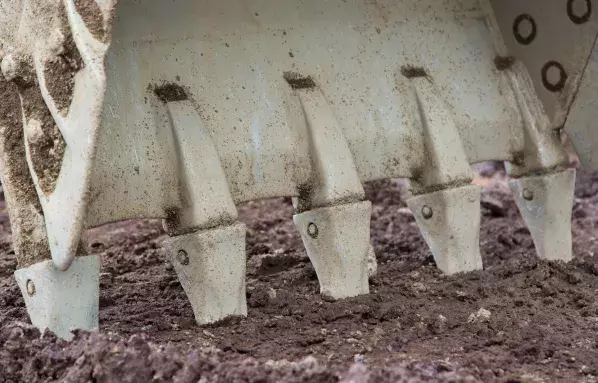
Iron ore, coal, limestone, fluxes and scrap are unloaded in the raw material area. They are classified, stored, crushed, grinded and handled for transport into the next production process. All these activities produce a combination of wear phenomena in the different machines and parts involved. Their service lifetime can be extended with different solutions, thanks to the cost reduction program from Castolin Eutectic.
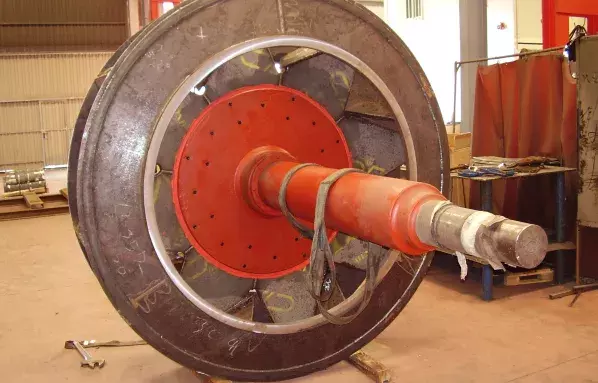
The first step for a good solution is a correct analysis
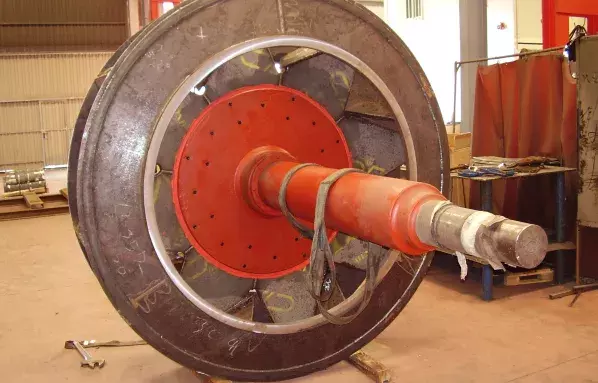
After processing the respective raw materials, they pass through the blast furnace, electric arc furnace (EAF) or basic oxygen furnace (BOF) to get pig iron or Steel. The first step for a good solution is a correct analysis. To facilitate this, we have created an analysis document that can easily be completed in collaboration with our technical delegate. The document reflects the most important parameters to be considered to develop in-house solutions to your wear problems.
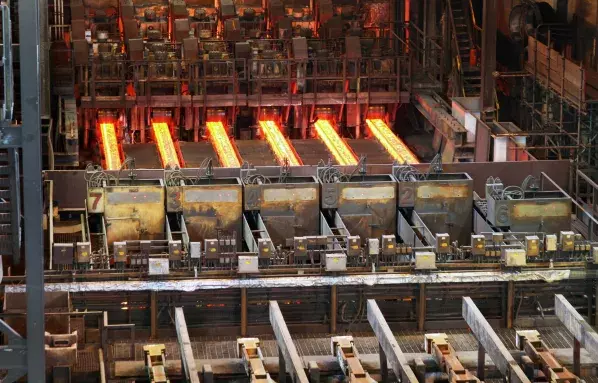
Repair Continous Casting Rollers according to OEM specifications
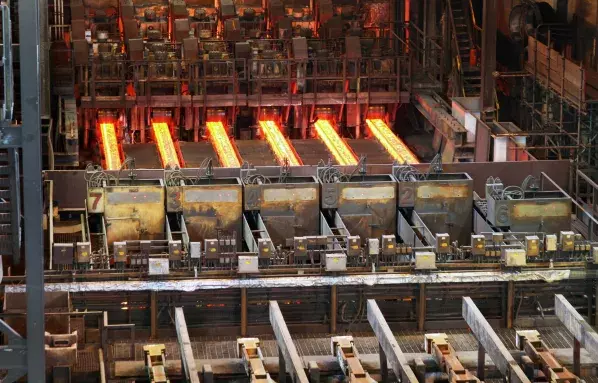
Continuous casting rolls are critical parts that are used for making the slabs, blooms or billets just after the tundish and moulds, at a very high temperature. The extreme working loads as well as the high temperature wear-out the rolls surface and, as a result, parts are damaged. Maintenance managers regularly have to decide to either scrap these expensive parts or try to repair them according to OEM specifications.
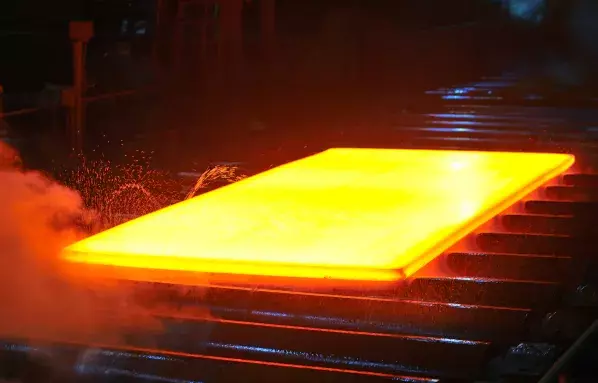
Rebuilding and repairing rolls for steel processing facilities
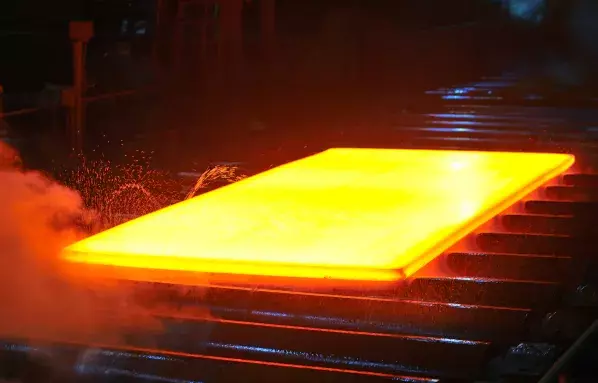
The semifinished products obtained after the continuous casting process have to be shaped before being comercialized. The first of these processes is hot rolling, from which sometimes final products are obtained and other times semifinished products intended for cold rolling or coating.
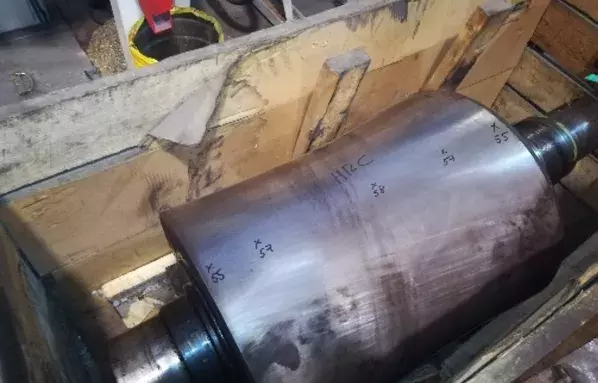
cooling the steel is a critical factor
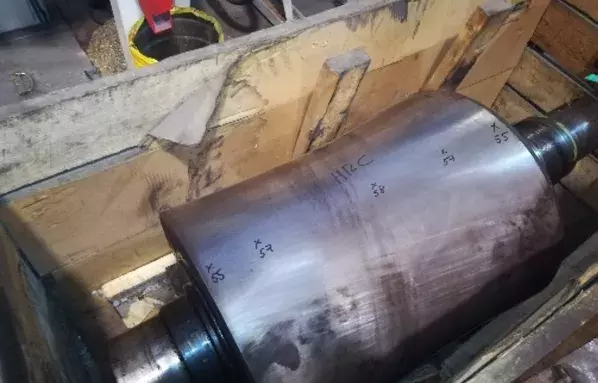
In all rolling processes, cooling the steel is a critical factor. The speed at which the rolled product is cooled will affect the mechanical properties of the steel. Cooling speed is controlled normally by spraying water on the steel as it passes through and/or leaves the mill, although occasionally the rolled steel is air-cooled using large fans.
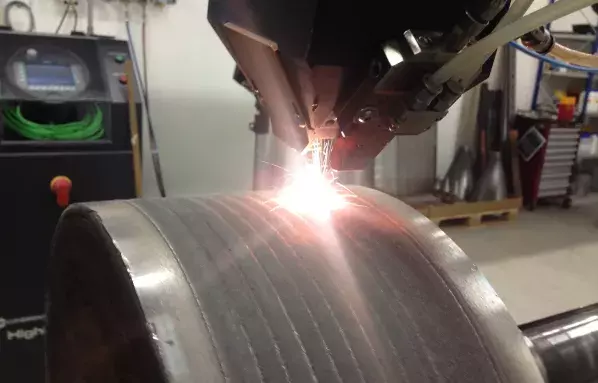
Rolls protected by laser cladding
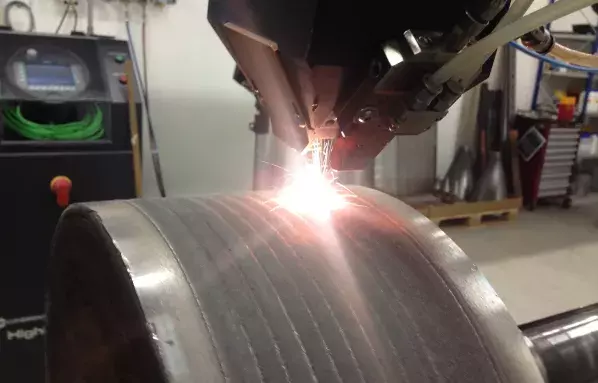
Since the installation of laser cladding technology in the Castolin Eutectic Services Centers the wear protection of key tools such as rolls and guides has been raised to a new level. The utilization of 8kW High Power Direct Diode (HPDD) with automation leads to flexible production and superior quality. In addition, the powerful laser enables high deposition rates that can reduce the cost of the cladding operation. Compared to standard welding techniques, the dissolution of the carbides and the dilution of the cladding material are the lowest that can be achieved. As a result, the wear-resistance is maximized and the service-life is longer. The unique broad beam (up to 23mm wide) produces a flat coated surface that minimizes subsequent machining or grinding. Rolls can often be used as welded without further processing. The low heat input of the laser process means the lowest distortion of large and thin wall parts that can easily be cladded.
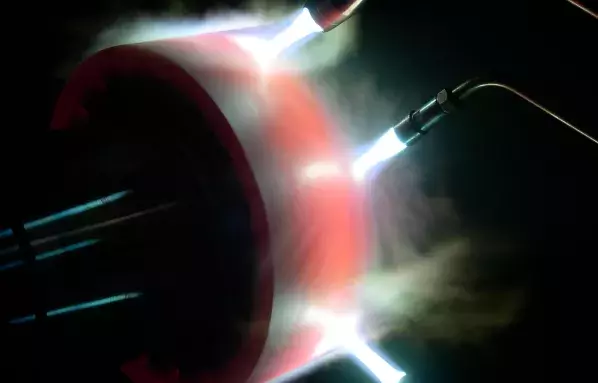
Rolls protected by spray & fuse
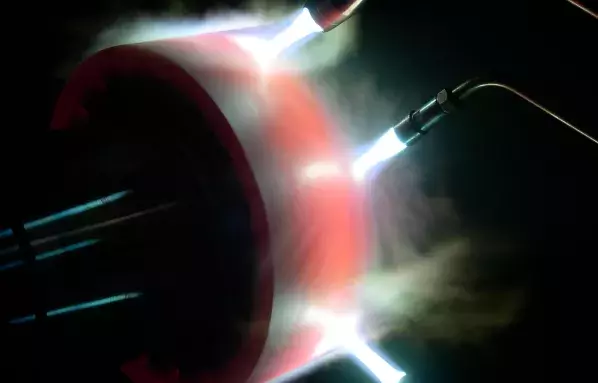
OEMs usually provide parts that have the surface coated with high wear resistant alloys such as Eutalloy® RW 12496. This coating is applied first by spraying a powder on the roller surface and then by fusing it just above the liquidus temperature. The process allows the coating to offer its best wear resistant properties and to perfectly bound on the steel substrate. On long and heavy parts, fusion is extremely difficult to be done correctly. Just after the spraying step, the part must be pre-heated homogeneously and kept in temperature while several torches fuse the powder all along the roll. In 2m long massive rolls, fusion may require up to 7 hours and any variation in temperature may result on an irregular surface quality. Since the part is exposed to very high temperature, deformation is also critical, especially on rolls made with thin wall tubes. Finally, if cooling is not well managed, thermal stresses can be so high that cracks may appear on the overlay. Our well-equipped service workshops as well as more than 10-years experience allow us to offer high quality overlays. Parts are coated by highly skilled operators that follow strict manufacturing methods. They regularly apply several powders according to what has been defined by OEMs.
Discover other industries
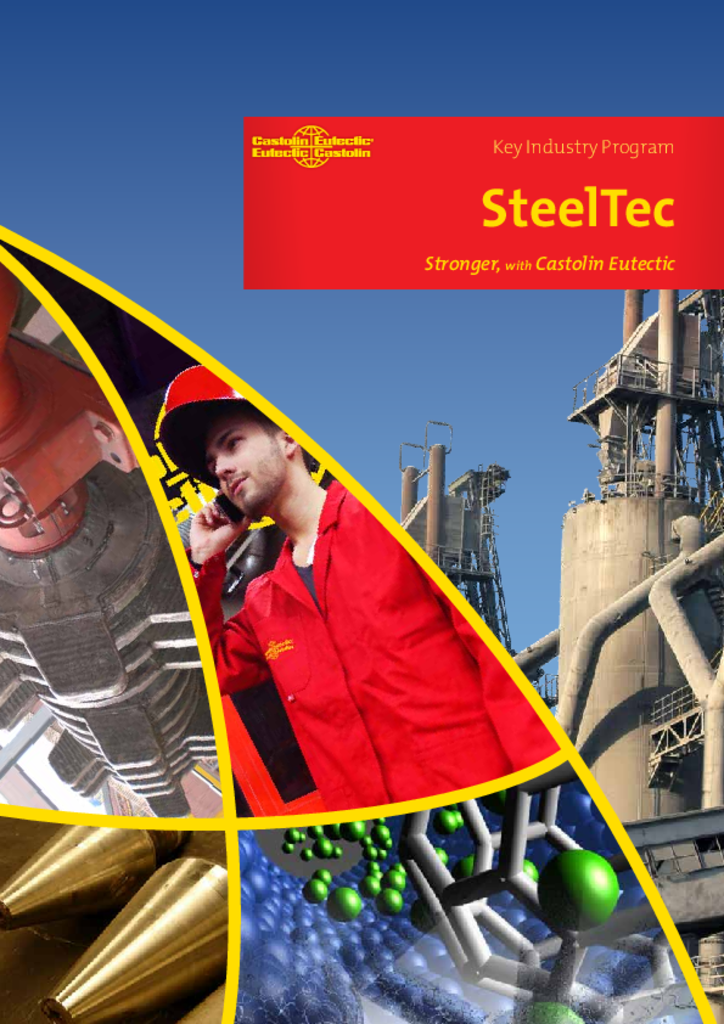
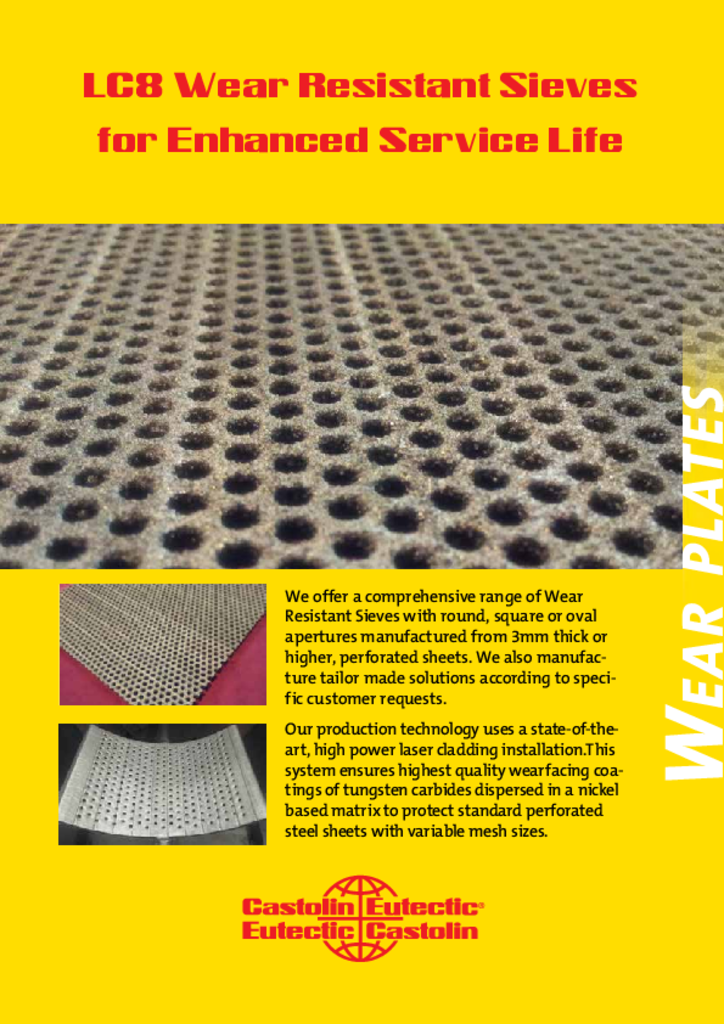